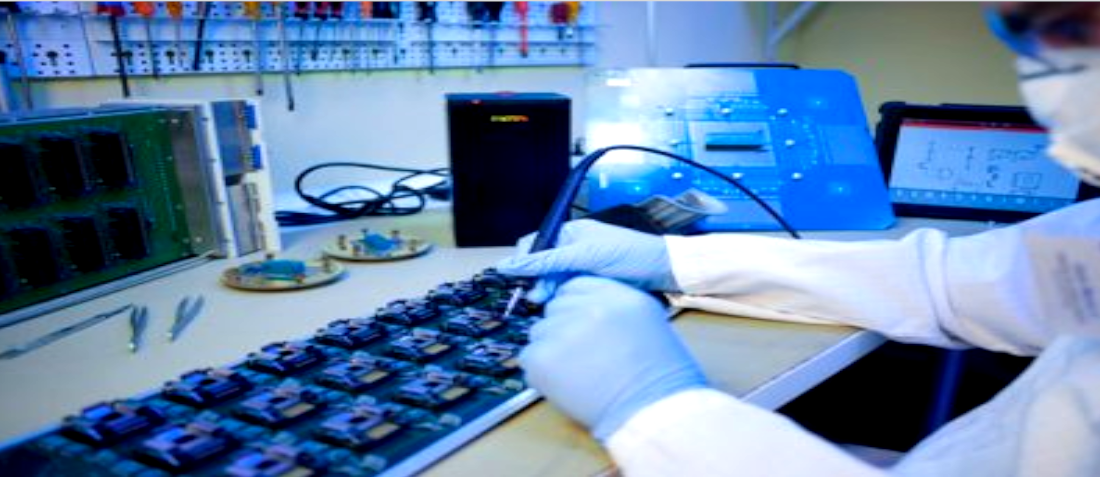
Burn-in Test Features
- Posted by Antonio Amigo
- On February 14, 2020
- 0
Burn-in test is an electrical stress test that typically employs voltage and/or temperature to accelerate the appearance of latent reliability defects in a device. The objective of burn-in is to eliminate all potential failure likely to occur at the early phase of the product life time (also called Infant Mortality Failure). It can easily be observed in a typical reliability bath tub curve as shown below.
Burn-in is the key screening step and is typically applied on 100% of the components in a lot.
A set of different test methods and requirements is defined for each product family, depending on the failure mechanisms that are targeted to be activated. Many of these mechanisms are dependent on product technology. For instance, the HTRB procedure (High-Temperature Reverse Bias) screens for mobile or temperature activated impurities within -and without- the device’s passivation layers; or SSOP (Steady-State Operating Power) which simulates the actual device operation but with accelerated conditions.
These tests are always performed in accordance with the corresponding test method, such as:
- MIL-STD-883, Method 1015, Method 1016 for integrated circuits
- MIL-STD-750 Method 1038, Method 1039, Method 1040, Method 1042 for discrete products
- MIL-STD-202 Method 108 for electronic and electrical parts
- JEP163, etc
During burn-in tests the components are subjected to stresses at or above maximum rated operating conditions and to a temperature specified by their quality level. The acceleration factor is determined by use of the Arrhenius reliability model as an effect of the temperature, by the duration of the test and by the activation energy (Ea) of each specific failure mode. Typically, a standard Ea single value is considered for the purpose of this test.
The acceleration factor activates specific failure modes thus leading to the elimination of defective parts.
GET IN TOUCH TODAY!
Do you have questions? Contact us!
Special burn-in boards where the samples are loaded are required for the burn-in process. These boards are inserted into the burn-in chamber which supplies the necessary biasing to the DUTs under stable and controlled temperature. The electrical bias applied may be either static or dynamic.
Burn-in tests allow to detect problem trends so as to prevent usage of reliability-critical components. Burn-in is the backbone of parts screening, the major vehicle to eliminate defective parts at the early phase of the product life and to ensure the product reliability.
FIGURE: Burn-in board design
GET IN TOUCH TODAY!
Do you have questions? Contact us!
- Burn-in Test Features - February 14, 2020
0 comments on Burn-in Test Features