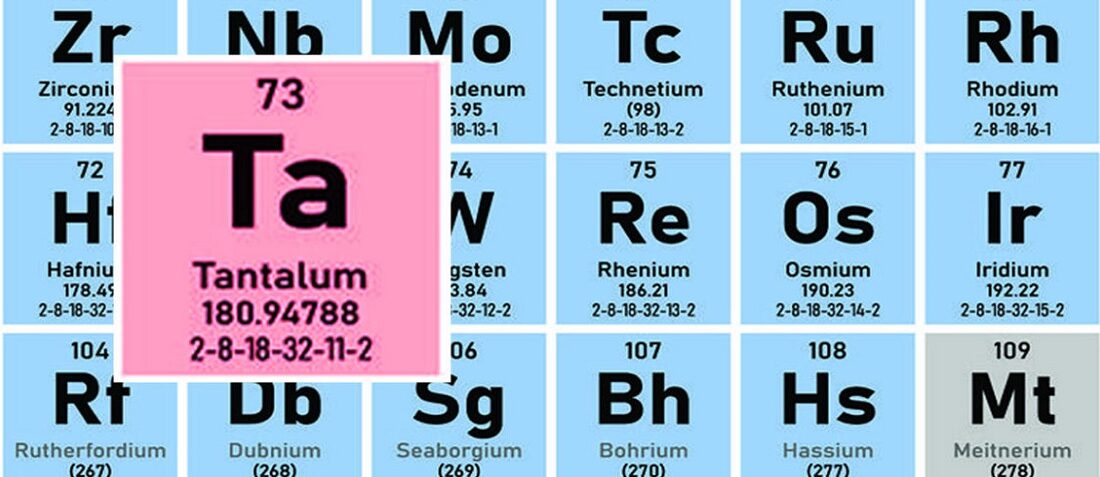
Tantalum Supply Routes for Mil-Spec Capacitors
- Posted by doEEEt Media Group
- On March 19, 2021
- 0
Tantalum Supply Routes for Mil-Spec Capacitors: From Ore, to Powder, to Part
Dennis Zogby from Paumanok Inc. describes tantalum capacitor supply chain in his article published by TTI Market Eye blog.
Tantalum, a key dielectric material for capacitors, is also considered a “strategic material” by the United States Defense Logistics Agency (DLA) because of its unique attributes. This article addresses the unique supply chain for tantalum capacitors that carry a military specification.
The Market for Tantalum: Electronics and Beyond
Paumanok Publications, Inc. estimates that, in 2019, approximately 5 million pounds of tantalum ores and concentrates were consumed in the global market in the form of engineered powder, wire, rods, ingots and sheets.
Of the 5 million pounds consumed, about 55 per cent will have been sold into the electronics industry, primarily in the form of anode for capacitor and as semiconductor targets. The remaining 45 per cent of the tantalum supply was consumed in alloy additives, industrial processing equipment, cemented carbides, fine chemicals and some additional speciality product lines.
A more granular look at tantalum consumption in electronics reveals that capacitors and semiconductors are the most important market drivers. However, additional minor markets (such as surface acoustical wave filters and thin-film resistors) also consume tantalum raw materials.
It is also important to note that demand from the electronics industry has averaged from 50 per cent to 70 per cent of total tantalum demand over the past 30 years.
Tantalum is also consumed in a myriad of additional industries outside of electronics, related to metallurgy and the creation of alloys and compounds. The most important usage is in the cemented carbide business, where tantalum is used as a grain inhibitor in professional cutting tools. Here, tantalum aids in controlling the microstructure and morphology of the carbide insert or wear part during sintering.
The Strategic Importance of Tantalum
Because of tantalum’s use as a hardener for cemented carbides (which are, in turn, used to cut steel), it has been considered a “strategic material” by the United States Department of Defense. The Defense Logistics Agency (DLA) stockpiled tantalum ore and powder for decades and was at one time a key supplier of tantalum to the electronics industry through auctions of their tantalum stocks. In fact, the DLA had a market share position in all Paumanok tantalum material studies prior to 2001.
After the price of the ore skyrocketed in the year 2000, the DLA made a significant return on investment for their annual sale of tantalum ore. After all stocks were sold off in 2001, the DLA never replenished its supply. In 2013, the DLA reported a shortfall of tantalum and suggested that it replenish its supply by 2017. This plan has been modified since but has not yet been implemented as of 2019.
Even though the use of tantalum as a hardener for cutting tools was considered strategic for the military of the past, its use as a dielectric in tantalum capacitors should be considered strategic for the military of the future. Tantalum is an excellent dielectric for use in space electronics because of its high heat handling capability and high capacitance in a small physical case size; several military specifications contain tantalum anodes (see table 1).
Table 1: Tantalum Capacitor Military Specifications
wdt_ID | MIL-PRF | Components |
---|---|---|
1 | MIL-PRF-55365 | Capacitor, Fixed, Electrolytic (Tantalum), Chip – Established Reliability, Non-Established Reliability and High Reliability |
4 | MIL-PRF-39006 | Capacitor, Fixed, Electrolytic (Nonsolid Electrolyte), Tantalum, Established Reliability |
7 | MIL-PRF-39003 | Capacitor, Fixed, Electrolytic (Solid Electrolyte), Tantalum, Established Reliability |
10 | MIL-PRF-49137 | Capacitor, Fixed, Electrolytic (Solid Electrolyte), Tantalum, Molded, Conformal Coated and Metal Cased with Plastic End-Fill, Non-Hermetically Sealed |
Why Aerospace and Defense Use Tantalum Capacitors
Capacitors are used for bypass, decoupling and filtering in all electronic circuits. Some circuits have demanding environmental requirements; in harsh environments where high temperatures accompany small form factors, tantalum is preferred.
In cases of mission-critical electronic systems for spacecraft and aircraft, capacitors that meet military specifications are preferred, especially when higher voltage circuits are involved (i.e. 25 and 35 volts) and combined with high capacitance requirements (2.2 to 1,000 microfarads) in small spaces.
The military specifications for tantalum capacitors have been in place for decades, and their performance is well-known and well-documented. This is why these components are preferred by military design engineers at the following companies (see Figure 2):
Figure 2: Top Consumers of Tantalum Capacitors for Defense and Space Applications, 2019
- Boeing
- Airbus EADS
- United Technologies
- Lockheed Martin
- General Dynamics
- BAE Systems
- Northrop Grumman
- Raytheon *
- Finmeccanica
- Thales *
- L-3 Technologies
- SAIC
- Rockwell Collins *
- Orbital Sciences Corp
- Crane
- Loral *
*Passive Component Intensive Defense Platforms
The Future Outlook for Tantalum in Defense
Tantalum capacitors are considered mission-critical to the future combat systems of the United States and its allies. The use of tantalum capacitors on spacecraft and satellites is well-documented in the Paumanok technical library, as are their use in defence aircraft. Key applications for tantalum in defence electronics include power supplies and munitions.
All the major tantalum capacitor operations that supply military-specification tantalum capacitors will be owned by foreign investment by the end of 2020.
The major vendor of tantalum capacitors to the United States military is Vishay Intertechnology, which acquired market access through its purchases of Sprague Electric, Mallory Capacitor, Transistor Capacitor and the wet tantalum capacitor operations of KEMET Corporation. KEMET is their closest competitor, with key competitive positions in almost every tantalum mil-spec. AVX also competes in mil-spec tantalum capacitors, but only in the most valuable segments. Recent market entrants include Firadec-Exxelia and CDE Electronics.
Tantalum Ore, Powder and Wire: Supply Chain Challenges
Ownership of the raw materials consumed in U.S. military-specification tantalum capacitors will also be outside of U.S. control by the end of 2020. Ore production has switched largely to central Africa in direct response to outside military and political influences on the supply chain.
Over the past decade (2010-2019), key hard- and soft-rock mining operations for tantalite have been either idled or permanently closed in Australia, Canada and Mozambique, leaving the majority of demand to be satisfied by mines and artisanal sources in DRC, Uganda and Rwanda. Ethiopia and Brazil continue to be the only two consistent ore vendors over the past 30 years (with long supply routes).
The sophisticated processing of tantalum into anode materials, especially high capacitance value per gram dielectrics, is largely dominated by Japanese and German businesses. The United States has one high CV/g powder processing plant serving the capacitor industry, KEMET Blue Powder Corporation in Nevada, which will come under Taiwanese ownership by the end of 2020.
In addition, tantalum has been the subject of international scrutiny for decades following the United Nations designation of this metal as a conflict mineral. This creates added layers of costs associated with legal bills, compliance and freight that other dielectrics and electronic components do not have.
Competing Technologies in Electronics
There are alternatives to tantalum in each industry where tantalum competes. However, the primary reason why industries use tantalum is because of its known reliability. This metal has been in continuous use for decades in multiple industries, especially defense and space electronics, so its performance and behavior are well documented.
The market for tantalum capacitors continues to exist because in electronic design, there are only so many ways to provide capacitance; each dielectric, especially tantalum, has a market value because the design engineer is limited in choice due to parameters of voltage, temperature, altitude, capacitance, frequency and volumetric efficiency.
Alternative Capacitor Technologies – As we have established, the electronics industry can account for between 50 percent and 70 percent of tantalum raw material consumption; this is the true variable that impacts global demand for the metal over time.
In electronics, tantalum capacitor substitutes include the ubiquitous and mass-produced high capacitance multilayered ceramic chip capacitor (MLCC); the conductive polymer, molded chip aluminum electrolytic capacitor (solid polymer aluminum); and the niobium oxide molded chip capacitor (NbO capacitor). All three of these alternative capacitor products have targeted tantalum capacitor displacement as a primary go-to-market strategy, and the vendors who produce these alternative dielectrics prey upon the shortcomings of the tantalum supply chain in order to propel their product forward through the market.
However, as is the case with MLCCs which have done the most to disrupt the tantalum supply, as capacitance increases, the available voltage decreases. This creates value opportunities for tantalum in voltages above 6.3 Vdc, so we find tantalum in many advanced electronic applications.
The solid polymer aluminum chip capacitor is also of great interest: it forms a threat to the larger case size tantalum chips because it offers high capacitance in a small form factor (just like tantalum) and offers the customer a product with an abundant and stable supply chain (bauxite or aluminum). However, the disadvantage is that the product line is limited, and the capacity to produce these products is also limited. The exact same advantages and disadvantages of solid polymer aluminum are evident in NbO capacitors as well.
Alternative Thin Film Technologies – In targets, tantalum is used as a thin film diffusion layer during the semiconductor manufacturing process. There are alternative targets that can be used here, such as tungsten, molybdenum and titanium, with the only disadvantage for tantalum being its challenging supply chain. However, tantalum’s advantage (according to primary sources in the semiconductor industry) is its known reliability, a critical factor in such an advanced process.
Tantalum also offers high thermal and electrical stability with copper; good adhesion to silicon; few grain boundaries; high bonding strength; and uniform grain thickness. These factors mean the engineer knows how the material will apply itself when it is sputtered.
What Will Happen Next in the Tantalum Supply Chain?
Electronics are the primary market driver for tantalum, and we expect to see its continued use in both capacitor anodes and as a diffusion layer in semiconductor manufacturing.
Tantalum capacitors, the major driver for the use of tantalum materials, will continue to be needed in the high-tech economy, especially in mission-critical circuits where known reliability and volumetric efficiency are key criteria in component selection.
Source: TTI Market Eye, Paumanok Inc.
- Space-Grade components available for immediate delivery - April 10, 2025
- Exclusive stock on doEEEt: How to access and request - April 10, 2025
- Managing EEE components for LEO and lower cost space missions - December 17, 2024
0 comments on Tantalum Supply Routes for Mil-Spec Capacitors