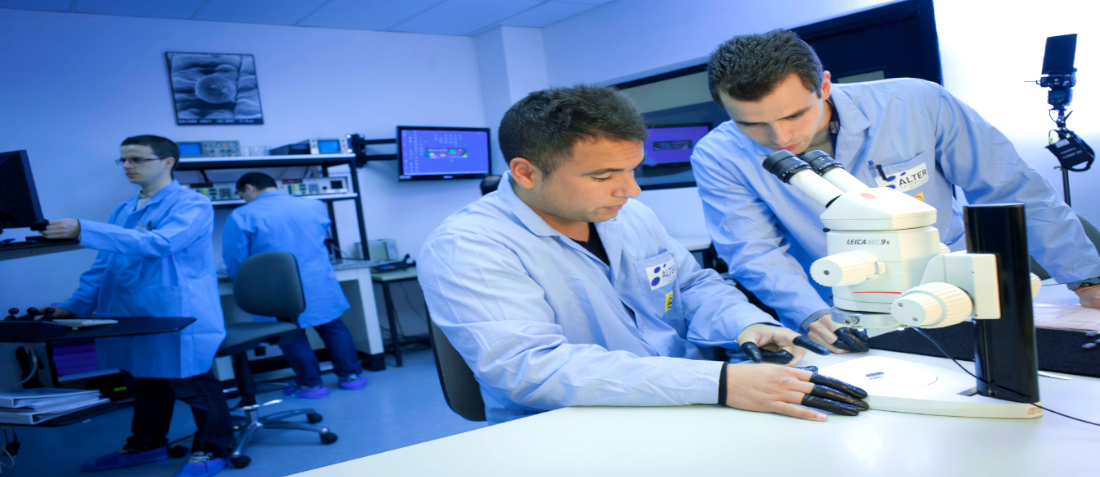
Steps to Procurement of Electronic Components
- Posted by Manuel Padial Pérez
- On November 20, 2020
- 0
The requirements about the needed quality level and additional product assurance activities on a lot of EEE components are established in documents like ECSS-Q-ST-60C, MSFC-STD-3012, NASA-STD-8739.10, ECSS-Q-ST-60-13C for commercial EEE components… and/or at the project level.
If additional activities are required, WHAT to do and HOW are included in documents like Generic Specifications, MIL-STD Test Methods, NASA EEE-INST-002, NASA PEM-INST-001…
ALTER TECHNOLOGY offers to his customers the whole procurement pack, leaving them to focus on their core activity (board/equipment assembly/manufacturing)
Fully compliant with the project requirements
Our commercial and technical expertise and experience allow us to recommend, select and supply components from good manufacturing sources (avoiding counterfeits). All EEE parts procured by us are fully inspected and tested to ensure they meet the requirements of the project/ customer contract. This enables us to confirm compliance with the:
- Quality and reliability requirements
- Cost constraints/budget
- Delivery schedule
The procurement can be provided through 2 basic different approaches:
Co-Ordinated Parts Procurement
Satellites with ESA as end customer and a prime contractor. This is a procurement approach where the agent receives the purchase orders for parts from various parts users, extracts and compiles the total need quantities per type and manufacturer, along with the necessary attrition (including DPA, LAT or QCI and radiation samples) and places the purchase orders at the corresponding manufacturers. Upon receipt of the flight parts by the CPPA, the quantities of the ordered parts will be tested as required and shipped to the individual users. The main features of the co-ordinated procurement are:
- CPPA (Coordinated Parts Procurement Agency) as the focal point interfaces for all parties involved in the EEE parts procurement.
- Users provide their DCL’s to the CPPA
- CPPA analyses and comments DCL with the aim to standardize part types and ensure compliance with PA requirements. All comments are discussed and agreed with the different users
- CPPA is the single interface with the manufacturer
- Users place purchase orders directly to CPPA
- CPPA co-ordinates PO placement to the manufacturers
- CPPA performs follow-up, inspections, and tests
- CPPA co-ordinates shipment to users
- Consolidates all user needs
- A wide number of advantages
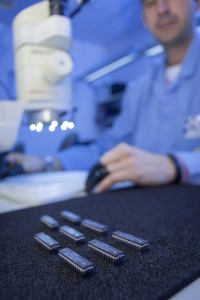
- Procurement specification preparation and integration
- Implementation and maintenance of the component
- Procurement and Control Plan preparation
- Obsolescence management
- Preparation of evaluation plans
- Preparation of screening plans
- Preparation of radiation test plans
- Radiation data analysis
- Performance of manufacturer audits
- Performance of capability assessments
- Reliability analysis of test results
- Component database management

Procurement Engineering
Full compliance with the project quality requirements
Selection and procurement of the correct EEE Parts are essential to meeting the hostile environmental, mechanical and radiation environments encountered in the space industry. To achieve this requires a high degree of engineering expertise and in other disciplines covering a wide range of components and technologies.
The services provided in each project are flexible depending on the project requirements and clients demands, among which we can highlight the following:
- Technical support, parts engineering and testing providing the right tools to the proper selection and subsequent use of EEE parts
- Parts and suppliers identification, definition and selection
- Documentation generation and seek of needed approvals to start the procurement (PAD, specifications, test plans, etc.)
- Parts ordering
- Follow-up
- ITAR management
- Guarantee full compliance with the project requirements
- Parts inspection and testing
- EEE parts product assurance, requirements understanding and specific services which are key factors in the project success
- Risk mitigation analysis
- Failure analysis
- Storage
- Non-conformance management
- Obsolescence management
Procurement Testing
When failure is not an option
The electronic components procured for space applications will be subjected to a variety of extreme environmental conditions but still have to function reliably. Whether they are exposed to vibration, extreme temperatures, or radiation, our experts select reliable components, inspecting and testing them to verify compliance with the specification requirements.
It is Alter Technology’s responsibility to assess the physical, electrical or environmental characteristic of the procured parts using the suitably calibrated equipment. Test processes shall be performed in accordance with specified procedures and test methods. The main tests performed by our test group include incoming inspection, DPA, screening, evaluation testing, lot acceptance test, relifing, etc.
External Info about EEE Parts:
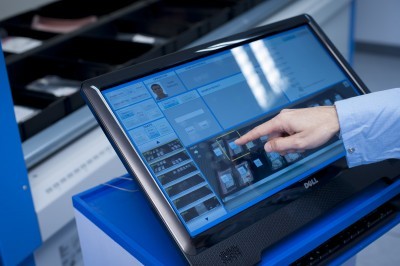
GET IN TOUCH TODAY!
Have questions? Contact us
- Hi-Rel Intermediate bus converter and point of load - December 11, 2021
- ASIC or FPGA, how to choose between them - October 25, 2021
- Ceramic Hermetic DDR2 SDRAM Memory avalaible for Space - September 13, 2021
0 comments on Steps to Procurement of Electronic Components