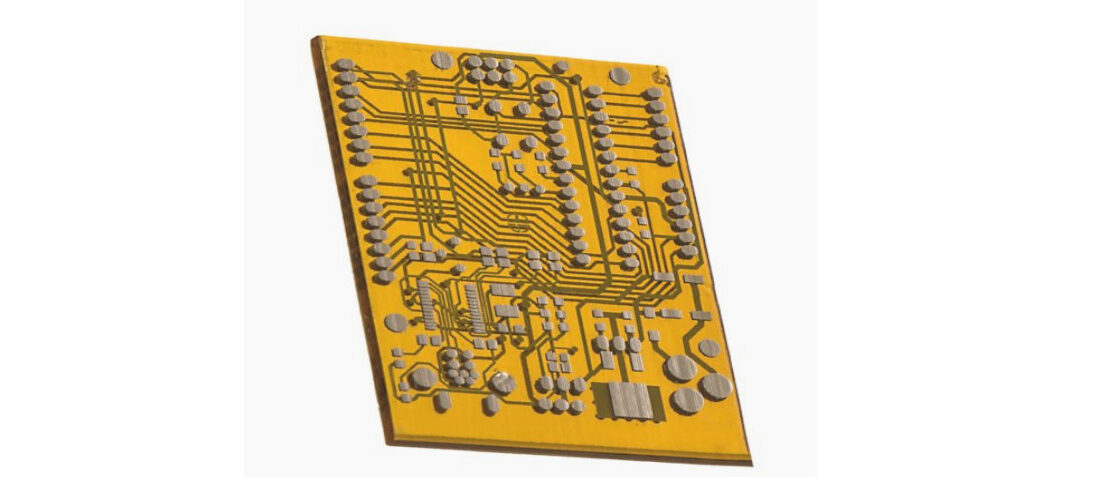
New PCBs on 3D printer, When are we going to print?
- Posted by Tomáš Zedníček
- On October 4, 2020
- 1
New PCBs on 3D printer
The development of PCB 3D printers is potentially linked with a number of topics and challenges that can be closely related to passive components. The question I asked myself about 3D PCB printing capabilities was also inhibited by the current shortage of certain passive components.
The large volume manufacturers have usually long term contracts and negotiation power to secure its sources, thus the main shortage of pain is usually with small and medium-size EMS manufacturers. Hence the question is:
“Will we be able in a close future to resolve a shortage of at least some passive components at small-medium volumes by direct 3D printing of PCBs?”
To get an answer I decided to contact Israel company Nano-dimension that was awarded by Productronica 2017 innovation prize for its DragonFly 2020 Pro PCB 3D printer. I was interested to find out if the PCB 3D printing process is ready to print passive components as part of its PCB printing process. Nano-Dimension invited me and Mr.Radek Nekarda, director of Amtech, a Czech assembly equipment specialist company, to visit their technology center in Israel and meet their experts to get a better understanding of the current PCB 3D printing capabilities.
The latest PCB 3D printer DragonFly 2020 Pro is the latest generation introduced to the market in Autumn 2017.
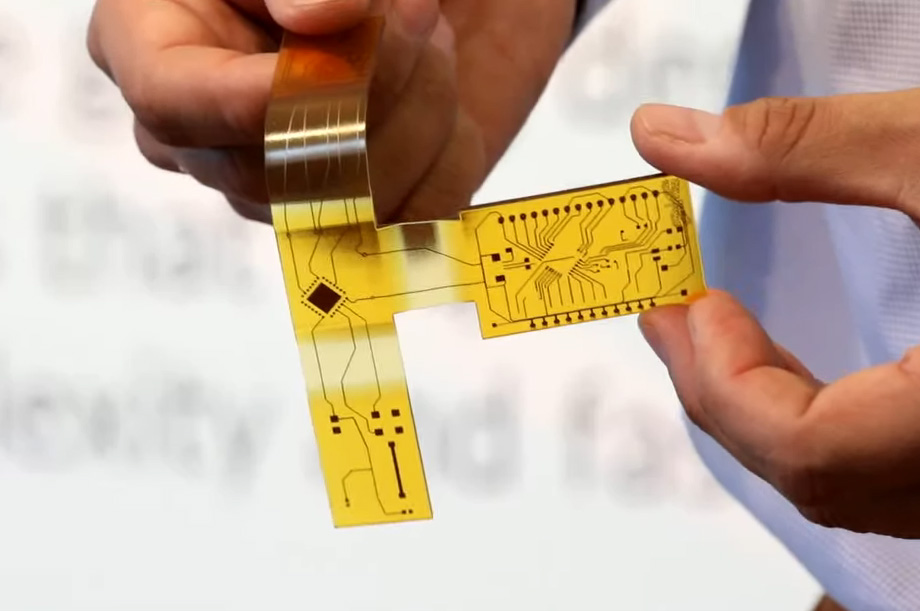
Fig. 1. and Fig.2 bottom right: PCB examples printed by DragonFly2020 Pro 3D printer; image credit: Nano-dimension
PCB 3D printers, How does it work?
The DragonFly 3D printer uses a precision additive printing process combining deposition of two types of inks – a non-conductive photo-polymer and a spot of conductive nano-silver ink. It‘s a full additive process, that means that both polymer and silver are step by step printed by drops and layers. The Z resolution of nano-silver ink 0.3μm and polymer dielectric 3μm is sufficient to print fine structures, conductive or insulated holes flexibly in 3D space volume.
The printed ink drop is immediately cured, but each material is cured differently. The photo-polymer by UV light and the nano-silver is sintered by heat. The silver sintering is necessary to melt the nanoparticles and thus make stable PCB electrical and mechanical properties.
The printed PCB can be assembled by automatic pick and place process, however, the current limitation is in temperature stress and the PCB can be mounted using low-temperature soldering process only around 140-150°C. The electrical dielectric features are close to FR4 PCB, mechanical is little worse, nevertheless still sufficient for prototyping work as the main target users of the 3D printer.
The printing process can be stopped anytime, discrete components can be inserted and the process continued. This gives another potential direction of the use of embedded components – not only passives.
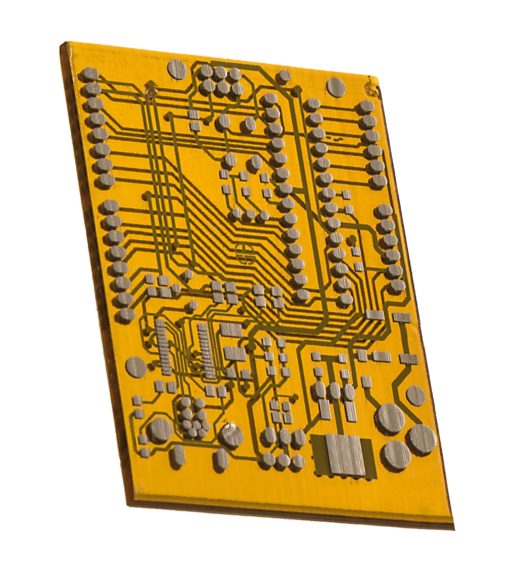
The key advantage is that you have a full flexibility for your imagination to realize 3D structures in a bulk volume of PCB. Thus you can design a structure that is difficult or impossible to make using conventional techniques such as a spiral coil from bottom PCB layer through all layers to the top. This can be of interest specifically for RF ID or antenna designers with unlimited shape modifications.
The DragonFly 2020 Pro accepts standard Gerber files, prepared by EDA PCB design softwares. 3D structures can be designed by SolidWorks with available plug-in that processes it and sends it directly to the 3D printer.
I asked Mr. Simon Fried, Nano-dimension president of North America and co-founder a few questions:
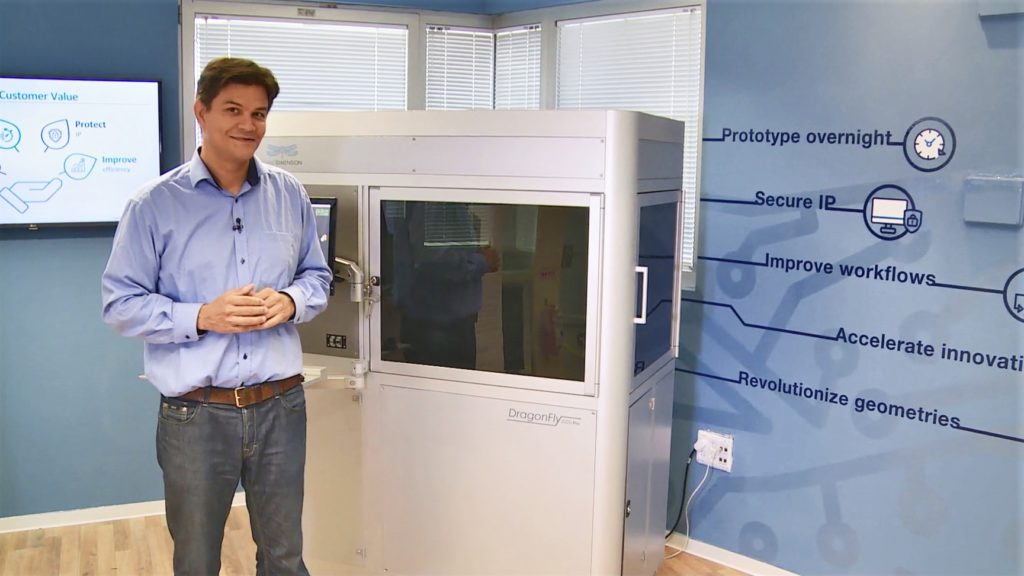
Fig.3. Mr. Simon Fried, Nano-dimension president of North America and co-founder in front of the DragonFly 2020 Pro PCB 3D printer; image credit: Nano-dimension
Selected Parameters of DragonFly 2020 Pro
- Max PCB dimension: 20×20 cm
- Max number of layers: up to 3mm, ~20+ layers
- Max thickness of one board: 3mm
- Typical layer thickness: Same as traditional PCB
- Min dimension between conductive path: 125 μm
- Layer Resolution: 3μm dielectric, 0.3 μm conductive silver ink
- Inks availability: proprietary Nano-dimension only at the moment, company count with opening it for other companies in future
- Printing cost: approx. 20-40 USD per layer of 10x10cm PCB, e.g. 200-400 USD of 10-layer 10x10cm PCB board
Summary and Conclusion
Returning back to my original question – obviously, as expected, the 3D PCB printers may not be ready soon to resolve the mass volume passive components, nevertheless, it made significant progress in past few years. In comparison to the “conventional” 3D printers – couple years ago they were considered as “prototyping tools” only and today we see some manufacturing floors full of industry grade 3D printers printing plastic or metallic structures. Thus, in the near future, we may count with 3D PCB printing development as a way forward for certain application area.
are we ready to print PCBs by 3D printing?
The current capabilities of PCB 3D printing can bring already its value to mainly fast and flexible prototyping work, but also in proving of new, innovative design thoughts that would be difficult or impossible to realize by currently available technologies. In addition, you can do everything “in-house” to protect your work without sharing it with third parties that have also its value especially for defense and military applications.
There are potential benefits also for “boring” passive components providing new freedom to try new constructions in PCB bulk 3D space without limitations. The additional feature is the capability to insert embedded components into the PCB to utilize technologies that are not possible to make by the 3D printing directly.
The 3D PCB printed is not yet dedicated to mass manufacturing (or even manufacturing) of PCBs. Nevertheless:
“The era of multi-material functional printing for electronics has ushered in the ability to significantly compress the time required to develop and prototype circuits, to de-risk the development process, to allow for more freedom and experimentation, to ensure that sensitive IP stays in the house for longer,” said Fried
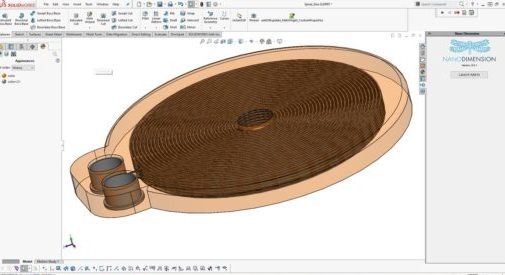
Fig.4. 3D spiral coil design in SolidWorks software ready for printing by DragonFly2020 Pro 3D printer; image credit: Nano-dimension
featured image:
- Why low ESR matters in capacitor design - May 24, 2021
- Voltage and Frequency Dependence on Resistors - March 6, 2021
- Permeability concept in Inductors - March 4, 2021
1 comments on New PCBs on 3D printer, When are we going to print?