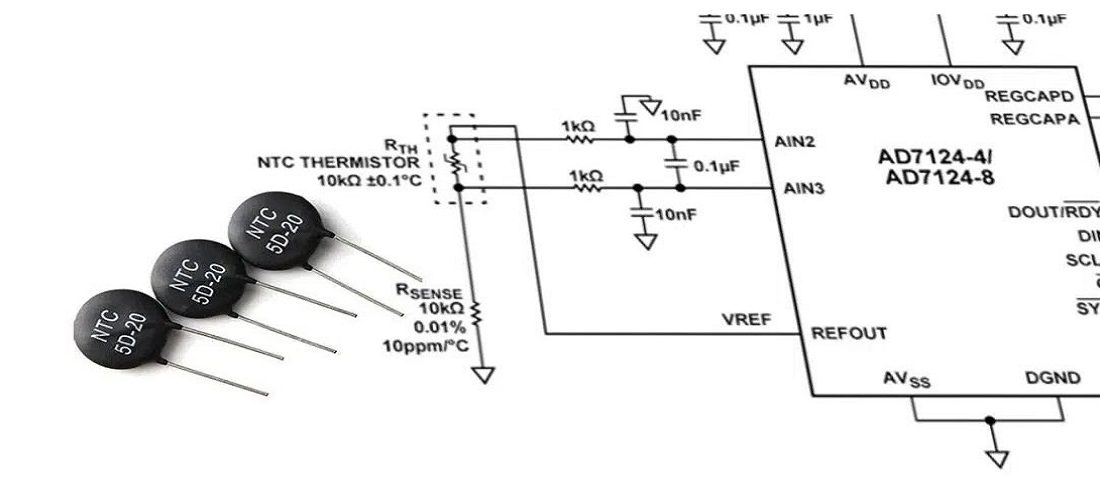
Thermistor-Based Temperature Sensing System Explained
- Posted by doEEEt Media Group
- On June 22, 2023
- 0
The Analogue Devices article written by Jellenie Rodriguez and Mary McCarthy discusses the history and design challenges for a thermistor-based temperature measurement system and how it compares with a resistance temperature detector (RTD)-based temperature measurement system.
It will also outline thermistor selection, configuration trade-offs, and the importance of sigma-delta analogue-to-digital converters (ADCs) in this application space.
Thermistors vs RTDs
Resistance Temperature Detector RTD is a type of resistor with resistance that varies as a function of temperature. Thermistors operate similarly to RTDs. Unlike RTDs with a positive temperature coefficient, thermistors can have positive or negative temperature coefficients.
A negative temperature coefficient (NTC) thermistor decreases its resistance as the temperature increases, while a positive temperature coefficient (PTC) thermistor increases its resistance as the temperature increases. Figure 1 shows the response characteristics of typical NTC and PTC thermistors and how they compare to an RTD curve.
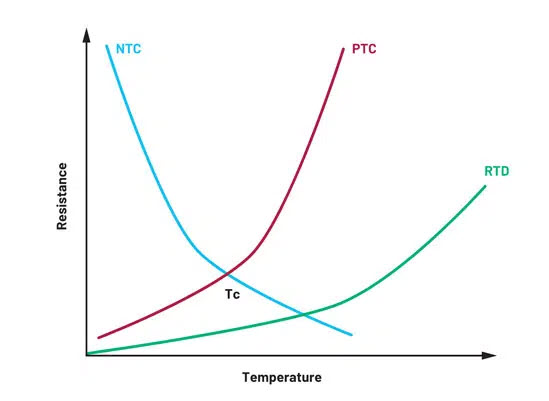
Figure 1. The response characteristics of thermistors vs. RTD.
The RTD curve is near linear in terms of temperature range, and the sensor covers a much more comprehensive temperature range (commonly –200°C to +850°C) than thermistors due to the thermistor’s nonlinear (exponential) characteristics. RTDs are usually available in a well-known standardized curve, while thermistor curves vary depending on the manufacturer. This article’s Thermistor Selection Guide section will discuss this in detail.
Thermistors are made up of composite materials, usually ceramic, polymer, or semiconductor (typically metal oxides), which are relatively more minor and more inexpensive but not as rugged when compared with RTDs, which are made of a pure metal (platinum, nickel, or copper). Thermistors can detect changes in temperature much faster than RTDs, delivering faster feedback. Thus, thermistors are commonly used sensors in applications that require low cost, small size, faster response rate, higher sensitivity, and with restricted temperature range, such as monitoring electronic equipment, households and building controls, scientific laboratories, or the cold-junction compensation used for thermocouples in commercial or industrial applications.
In most cases, NTC thermistors are used in precision temperature measurement applications rather than PTC thermistors. A few available PTC thermistors are used in overcurrent input protection circuits or as resettable fuses for safety applications. The resistance-to-temperature curve of a PTC thermistor exhibits a tiny NTC region until its switching point (or Curie point) is reached, above which a dramatic increase in resistance of several orders of magnitude occurs within a span of a few degrees Celsius. So, during an overcurrent condition, the PTC thermistor will have a high amount of self-heating beyond the switching temperature, and its resistance will increase dramatically, resulting in a reduced current being input to the system and preventing damage. The switching point for a PTC thermistor is typically between 60°C and 120°C, which is unsuitable for monitoring temperature measurements in a wide range of applications. This article focuses on NTC thermistors that can typically measure or monitor temperature from –80°C to +150°C. NTC thermistors have nominal resistances at 25°C, ranging from a few ohms to 10 MΩ. As shown in Figure 1, the resistance changes per degree Celsius are more significant for a thermistor vs an RTD. The high sensitivity and high resistance values of thermistors make their front-end circuitry much simpler than RTDs, as a thermistor does not need any unique wiring configurations such as 3-wire or 4-wire to compensate for lead resistance. Thermistor design only uses a simple 2-wire format.
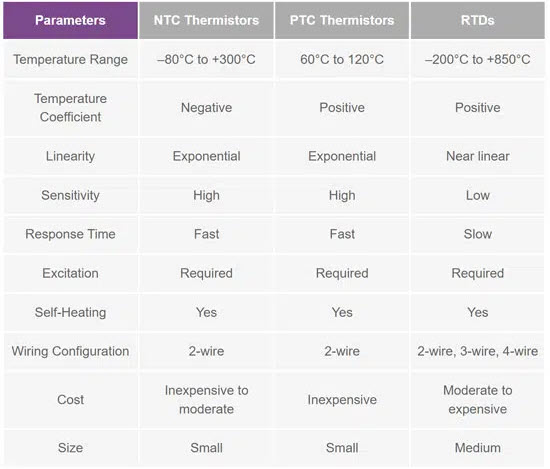
Table 1 shows the pros and cons of RTDs, NTC, and PTC thermistors.
Thermistor-Based Temperature Measurement Challenges
A high-precision and accurate thermistor-based temperature measurement requires precise signal conditioning, analogue-to-digital conversion, linearization, and compensation, as shown in Figure 2. Though the signal chain looks simple, several complex factors are involved that also impact overall system board size, cost, and performance. Several integrated solutions are available in ADI’s precision ADC portfolio, such as the AD7124-4/AD7124-8, which offer multiple benefits when designing a temperature system since most of the building blocks required in the application are built in. However, different challenges are involved in designing and optimizing a thermistor-based temperature measurement solution.
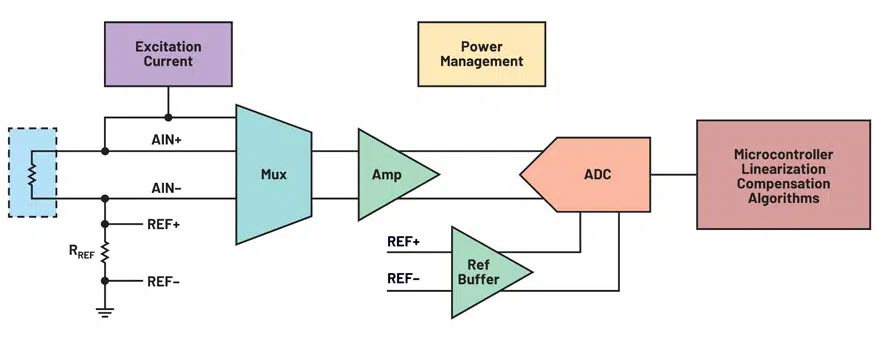
Figure 2. A typical NTC thermistor measurement signal chain block.
Challenges include:
- A wide range of thermistors are available in the market.
- How do I select the right one for my application?
- Like RTDs, thermistors are passive devices that do not produce an electrical output independently. Excitation current or voltage measures the sensor’s resistance by passing a small electrical current through the sensor to generate a voltage.
- How do I select the current/voltage?
- How should the thermistor signal be conditioned?
- How do I adjust the above variables so the converter or other building blocks are used within their specification?
- Connecting multiple thermistors in a system: How are the sensors connected? Can some blocks be shared among the different sensors? What is the impact to the overall system performance?
- A primary concern about thermistors is their nonlinear response and system accuracy.
- What is the expected error for my design?
- What linearization and compensation techniques are used to achieve the target performance?
This article discusses these challenges and provides advice on how to resolve these issues and further ease the journey in designing such a system.
Thermistor Selection Guide
A broad selection of NTC thermistors is available today, so selecting a specific thermistor for your application can be quite challenging. Note that thermistors are listed by their nominal value, the nominal resistance at 25°C. So, a 10 kΩ thermistor has a nominal resistance of 10 kΩ at 25°C. Thermistors are available with nominal or base resistance values from a few ohms to 10 MΩ. Thermistors with low nominal resistance (10 kΩ or less nominal resistance) typically support a lower temperature range, such as –50°C to +70°C. Thermistors with higher nominal resistance support temperatures up to 300°C.
The thermistor element is made from metal oxides. Thermistors are available in bead, radial, and SMD forms. Bead thermistors are epoxy-coated or glass encapsulated for extra protection. Epoxy-coated bead thermistors, radial, and SMD thermistors are suitable for temperatures up to 150°C. Glass-coated bead thermistors are suitable for high-temperature measurements. The coating/packaging for all types also prevents corrosion. Some thermistors will also have additional housing to further protection in harsh environments. Bead thermistors have a faster response time vs radial/SMD thermistors. However, they are not as robust. So, the thermistor type depends on the end application and the environment in which the thermistor will reside. The long-term stability of a thermistor is dependent on the materials it is made from, along with its packaging and construction. For example, an epoxy-coated NTC thermistor can change by 0.2°C per year, while a hermetically sealed one changes by only 0.02°C per year.
Thermistors have differing accuracy. Standard thermistors typically have an accuracy of 0.5°C to 1.5°C. Thermistors have a tolerance on their nominal resistance value and on their beta value (25°C to 50°C/85°C relationship). Note that the beta value of a thermistor is dependent on the manufacturer. For example, 10 kΩ NTC thermistors from different manufacturers will have different beta values. For higher accuracy systems, thermistors such as the Omega™ 44xxx series can be used. These have an accuracy of 0.1°C or 0.2°C over a temperature range of 0°C to 70°C. So, the temperature range being measured, along with the accuracy required over the temperature range, determines whether a thermistor is suitable for the application. Note that the more accurate the Omega 44xxx series is, the higher its cost.
Therefore, the thermistor to be used depends on the following:
- Temperature range being measured
- Accuracy required
- Environment in which the thermistor is used
- Long-term stability
Linearization: Beta vs. Steinhart-Hart Equation
A beta value is commonly used to convert from resistance to degrees Celsius. The beta value is determined by knowing two temperature points and the corresponding resistance at each temperature point.
![eq.[1]](https://www.doeeet.com/content/wp-content/uploads/2023/06/eq.1.jpg)
eq.[1]
Where:
- RT1 = Resistance at Temperature 1
- RT2 = Resistance at Temperature 2
- T1 = Temperature 1 (K) T2 = Temperature 2 (K)
The data sheet for the thermistor normally lists the beta value for two cases:
- The two temperatures being 25°C and 50°C
- The two temperatures being 25°C and 85°C
The user uses the beta value closest to the temperature range used in the design. Most thermistor data sheets list the beta value along with the resistance tolerance at 25°C and the tolerance of the beta value.
Higher accuracy thermistors such as the Omega 44xxx series and higher accuracy end solutions use the Steinhart-Hart equation to convert from resistance to degrees Celsius. From Equation 2, three constants—A, B, and C—are needed, which are provided again by the sensor manufacturer. As the coefficients for the equation are generated using three temperature points, the resulting equation minimizes the error introduced due to linearization (the error due to linearization is typically 0.02°C).
![eq.[2]](https://www.doeeet.com/content/wp-content/uploads/2023/06/eq.2.jpg)
eq.[2]
Where:
- A, B, and C are constants derived from three temperature test points.
- R = Thermistor’s resistance in Ω
- T = Temperature in degrees K
Current/Voltage Excitation
Figure 3 shows the current excitation of the sensor. An excitation current is applied to the thermistor, and the same current is applied to a precision resistor, the precision resistor being used as the reference for the measurement. The reference resistor must have a value greater than or equal to the highest resistance value of the thermistor (dependent on the minimum temperature being measured in the system).
When choosing the excitation current’s magnitude, the thermistor’s maximum resistance must again be considered. This ensures that the voltage generated across the sensor and the reference resistor is always acceptable for the electronics. Excitation current sources require some headroom or output compliance. If the thermistor has a large resistance at the minimum measured temperature, this leads to a very low excitation current value. Therefore, the voltage generated across the thermistor at hot temperatures is small. A programmable gain stage could be used to optimize the measurement of these low-level signals. However, the gain needs to be programmed dynamically as the signal level from the thermistor changes significantly over temperature.
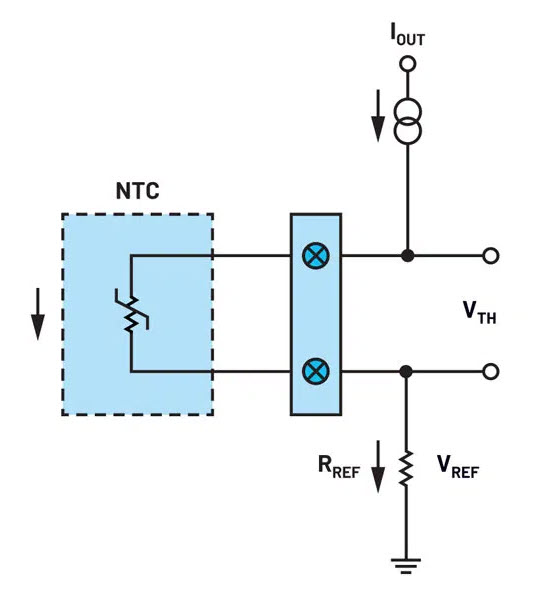
Figure 3. The current excitation of a thermistor.
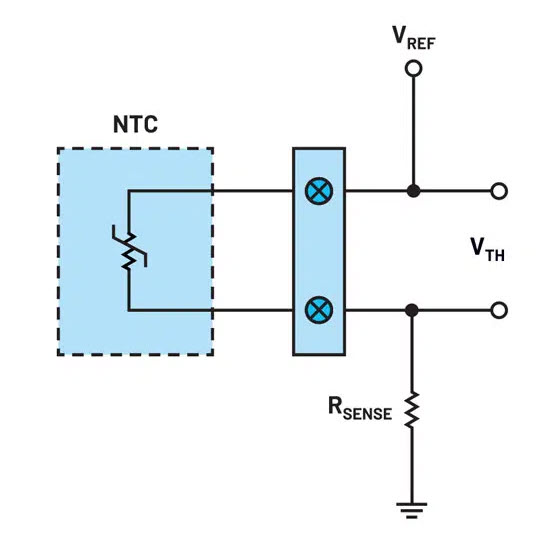
Figure 4. The voltage excitation of a thermistor
Another option is to set the gain but use a dynamic excitation current. So, as the signal level from the thermistor changes, the excitation current value is changed dynamically so that the voltage generated across the thermistor is within the electronics’ specified input range. The user must ensure that the voltage developed across the reference resistor is also acceptable for the electronics. Both options require a high level of control, continuously monitoring the voltage across the thermistor to ensure that the electronics can measure the signal. Is there a more straightforward option? Let’s look at voltage excitation – Figure 4.
When the thermistor is excited by a constant voltage, the current through the thermistor will scale automatically as the thermistor resistance changes. Rather than using a reference resistor, a precision sense resistor is now used; its purpose is to calculate the current flowing through the thermistor so that the thermistor resistance can be calculated. The excitation voltage as the ADC reference, eliminating the need for a gain stage. There is no workload for the processor regarding monitoring the voltage across the thermistor, determining whether the electronics can measure the signal level, and calculating what the gain/excitation current value needs to be adjusted to. This is the approach used in this article.
Thermistor Resistance Range/Excitation
If the thermistor nominal resistance and resistance range are small, either voltage or current excitation can be used. In this case, the excitation current and gain can be fixed. So, the circuit will be as shown in Figure 3. This method is helpful as the current flowing through the sensor and reference resistor can be controlled, which is valuable in low-power applications. Also, the self-heating of the thermistor is minimized.
Voltage excitation for a thermistor with low nominal resistance can also be used. However, the user must ensure that the current through the sensor is not too large for the sensor itself or the application at any time.
When using thermistors with considerable nominal resistance and temperature range, voltage excitation leads to a more straightforward implementation. The more considerable minor resistance ensures that the little current is reasonable. However, the designer needs to ensure that the wind is acceptable over the complete temperature range supported by the application.
Importance of Sigma-Delta ADCs in Thermistor-Based Applications
Sigma-delta ADCs offer multiple benefits when designing thermistor measurement systems. Firstly, as sigma-delta ADCs oversample the analogue input, external filtering is minimized, a simple RC filter being the only requirement. They offer flexibility in terms of choice of filter type and output data rate. The inbuilt digital filtering can reject any interference from the mains power supply in mains-operated designs. A 24-bit part such as the AD7124-4/AD7124-8 has a maximum peak-to-peak resolution of 21.7 bits, so they offer a high resolution.
Other benefits are:
- The wide common-mode range for the analogue inputs
- The wide common-mode range for the reference inputs
- Ability to support ratiometric configurations
Some sigma-delta ADCs are highly integrated and include the following:
- PGA
- Internal reference
- Reference/analogue input buffers
- Calibration functions
Using sigma-delta ADCs simplifies the thermistor design significantly, reducing the BOM, system cost, board space, and time to market.
For this article, the AD7124-4/AD7124-8 is used as the ADC, as they are low noise, low current precision ADCs with an integrated PGA, embedded reference, analogue input, and connection buffers.
Thermistor Circuit Configuration—Ratiometric Configuration
Whether you use an excitation current or an excitation voltage, it is recommended to use a ratiometric configuration wherein the reference and sensor voltages are derived from the same excitation source. This means that any variations in the excitation source will not affect the accuracy of the measurement.
Figure 5 shows a constant excitation current supplying the thermistor and a precision resistor RREF, the voltage generated across RREF being the reference voltage for the thermistor measurement. The excitation current does not need to be accurate and could be less stable since any errors in the excitation current will be cancelled in this configuration. An excitation current is usually preferred over voltage excitation due to its superior sensitivity control and better noise immunity when the sensor is in a remote area. This biasing technique uses RTDs or thermistors with low resistance values.
However, for thermistors with higher resistance values and sensitivity, signal levels generated will be more significant per change in temperature, so voltage excitation is used. For example, a ten kΩ thermistor has a resistance of 10 kΩ at 25°C. At −50°C, the NTC thermistor resistance is 441.117 kΩ. The minor excitation current of 50 µA provided by the AD7124-4/AD7124-8 generates a voltage of 441.117 kΩ × 50 µA = 22 V, which is too high and outside the operating range of most available ADCs used in this application space. Thermistors are also usually connected or located near the electronics, so the noise immunity advantage of an excitation current is not needed.
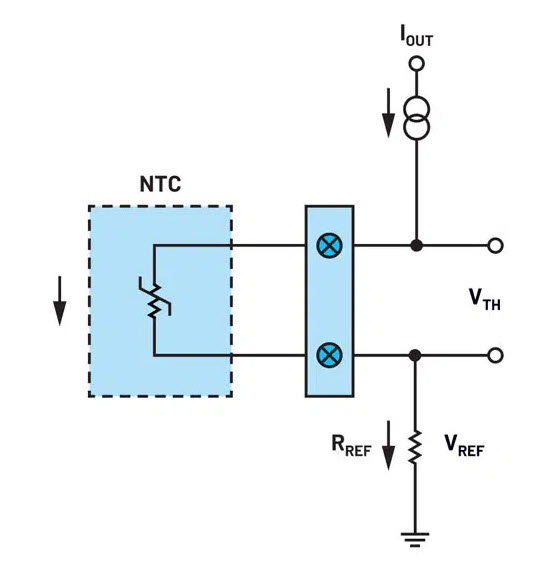
Figure 5. NTC thermistor configuration with a constant current source.
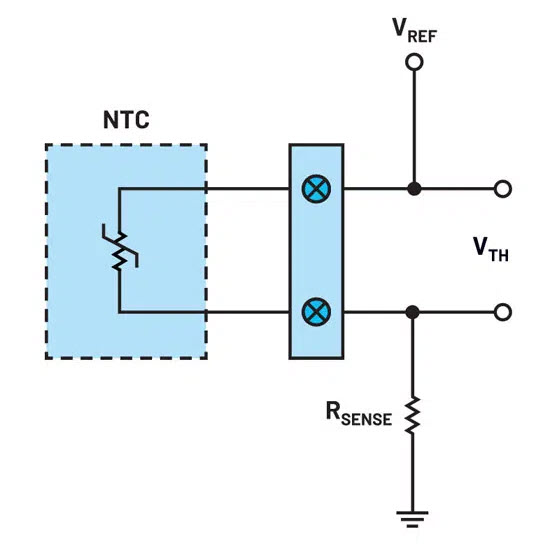
Figure 6. NTC thermistor configuration with a voltage divider circuit.
Figure 6 shows a constant excitation voltage used to generate a voltage across the NTC thermistor. Adding a series sense resistor as a voltage divider circuit will limit the current flow across the thermistor at its minimum resistance value. In this configuration, the value of the sense resistor, RSENSE, must be equal to the magnitude of the thermistor’s resistance at the base temperature of 25°C so that the output voltage will be set at the midscale value of the reference voltage when it is at its nominal temperature of 25°C. So again, if a ten kΩ thermistor that has a resistance of 10 kΩ at 25°C is used, the RSENSE must be equal to 10 kΩ. When the temperature changes, the resistance of the NTC thermistor also changes, and the fraction of the excitation voltage across the thermistor also changes, producing an output voltage proportional to the NTC thermistor resistance.
Suppose the selected reference voltage is used to supply the thermistor, and RSENSE is the same reference as the ADC reference used for the measurement. In that case, the system is configured in a ratiometric size (Figure 7) so that any errors associated with the excitation voltage source will be removed.
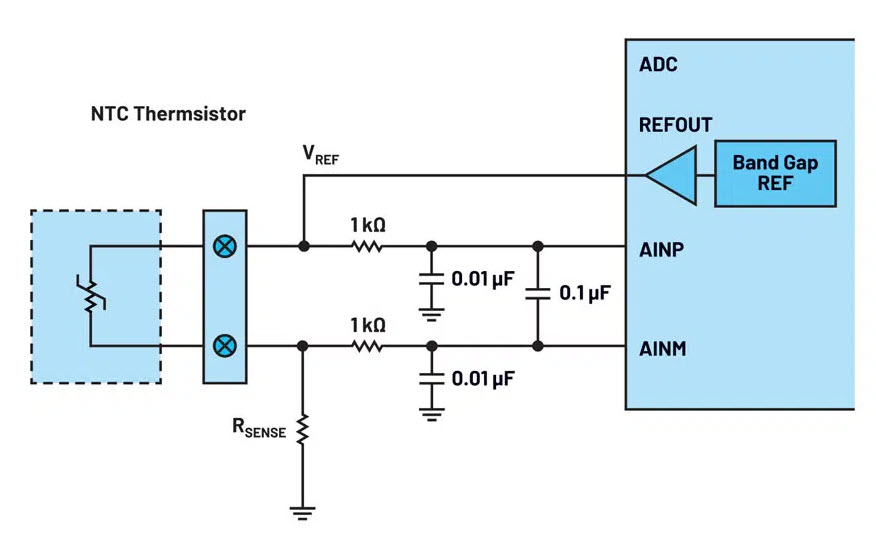
Figure 7. A thermistor ratiometric configuration measurement.

Figure 8. Multiple thermistors’ analog input configuration measurements.
Note that the sense resistor (voltage excitation) or reference resistor (current excitation) needs low initial tolerance and low drift as both variables contribute to the overall system accuracy.
When multiple thermistors are used, a single excitation voltage can be used. However, each thermistor must have its precision sense resistor, as shown in Figure 8. Another option is to use an external mux or switches with low resistance, which allows sharing of a single precision sense resistor. Each thermistor requires some settling time in the measurement when using this configuration.
- Space-Grade components available for immediate delivery - April 10, 2025
- Exclusive stock on doEEEt: How to access and request - April 10, 2025
- Managing EEE components for LEO and lower cost space missions - December 17, 2024
0 comments on Thermistor-Based Temperature Sensing System Explained