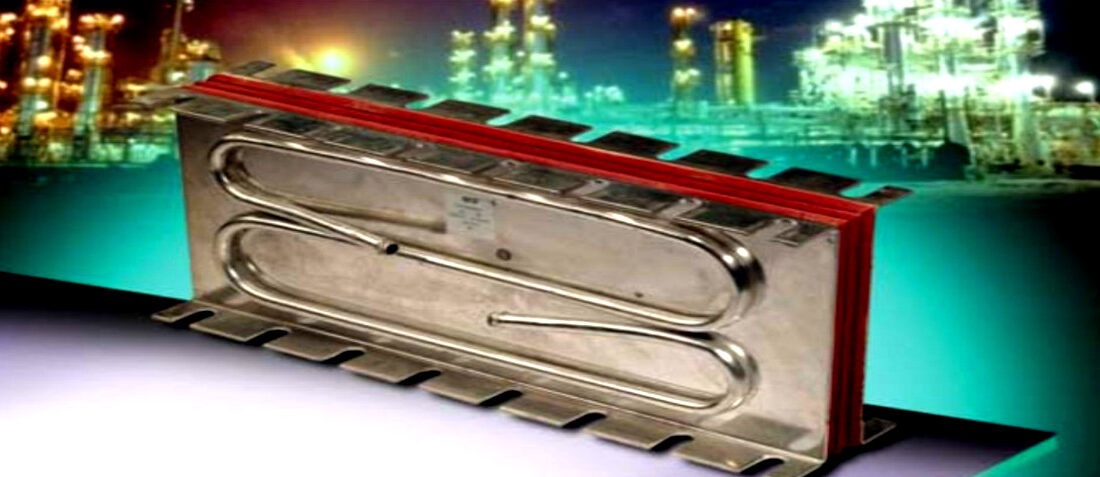
The anatomy of a water cooled capacitor
- Posted by doEEEt Media Group
- On July 29, 2020
- 0
Ceramic and film capacitors are widely used in power electronic systems because they can handle high operating currents. Heat is generated in these components mainly through dielectric losses. Heat is also generated at the points of connection between the leads and the dielectric material. This heat is usually referred to as connection losses. Due to the high levels of currents that these components are exposed to, considerable amount of heat is generated. Cooling such a capacitor helps to enhance its performance as well as its reliability.
Methods for cooling capacitors
Capacitors for use in high-power and high-frequency applications are cooled using various methods. The most common cooling methods include self-cooling, forced ventilation, and liquid cooling. These methods are all aimed at ensuring that the temperature of a capacitor is maintained within the acceptable limits.
In self-cooling method, cooling is achieved through natural air circulation. This method requires that the ambient air temperature is maintained below a specific value, typically 40oC. Self-cooling is mostly used for cooling capacitor banks and is unsuitable for applications where the component can generate extreme amounts of heat.
The forced ventilation cooling method is more effective as compared to self-cooling. In this method, cooling air is forcefully directed onto a capacitor using a suitable device. Most forced-air cooling systems utilize ventilators. The temperature of the outflowing air should not exceed the value specified by the manufacturer, typically 40oC.
The effectiveness of a forced-air cooling system depends on the design of the capacitor. Some forced-air cooled capacitors have fins that help to increase the surface area for heat dissipation. Most of today’s forced-air cooled capacitors have center air channels for improved cooling efficiency.
Design and characteristics of water cooled capacitors
In high-current and high-frequency applications, water cooled film/foil, metallized film, and ceramic capacitors are used for a wide range of applications including filtering and tank circuit applications. The design of these capacitors makes them suitable for high-power, high-current, and high-frequency applications such as broadcast transmitter, induction heating, melting, and high-frequency welding systems.
Using banks of small capacitors helps to distribute the heat generated by capacitors. Banks of small capacitors are commonly used in power electronic circuits. Although this approach helps in thermal management, it is not a suitable option for applications with limited space. Capacitors with integrated water cooling systems are suitable for such applications. Using water-cooled capacitors also helps to reduce the cost and the number of components used.
Film and ceramic capacitors with integrated liquid cooling systems are increasingly becoming popular for high-current applications. The liquids that are commonly used in such systems are water, a mixture of water and chemical solutions, and de-ionized water. Liquid-cooled capacitors are a suitable choice for power electronic circuits with high energy densities. This cooling method is suitable for applications where the ambient temperature does not exceed the value specified by the manufacturer.
Some liquid cooling systems are designed to cool the components at the surface while others can cool them inside the casing. Most traditional cooling systems are designed to cool a capacitor by passing the cooling medium over the external casing of a component. In most modern water cooled capacitors, the cooling medium passes through the interior of the component. These modern water-cooled capacitors are more efficient compared to their predecessors.
There are various ways of achieving cooling in water cooled capacitors. The most commonly used designs are transverse cooling and foil cooling. In transverse cooling, the cooling system is insulated from the elements of the capacitor. The coils are inserted between the elements of a component. These cooling coils are then connected to the tubes of the cooling system through which water flows.
In foil cooling systems, one plate of a capacitor is connected to the cooling tube system. This plate is used both for heat dissipation and current conduction. Since the water channel and the casing are live, extra caution is required when handling these components. To make these capacitors safer for use, the water channel and the casing are insulated from earth. In addition, insulated tubes are used to feed the system with water. The length of these tubes is determined by the specific resistance of the cooling water and the operating voltage.
The temperature of the water at the outlet of a cooling system is determined by the temperature at the inlet as well as the flow rate. This temperature should not exceed the value specified by the manufacturer. In addition, the flow rate and the pressure of the water should be within the range specified by the manufacturer.
In applications where many water cooled capacitors are used, the cooling circuit can be connected either in parallel or in series. The parallel connection has a low pressure drop and produces a high cooling effect. In serially connected cooling systems, there is a significant drop in water pressure and a high initial pressure is required. The temperature, pressure, and water quality requirements are specified by the manufacturer.
The effectiveness of water cooling is dependent on the properties of the water used. The water for use in water cooled capacitors should be chemically neutral, mechanically pure, and its electrical conductivity should not exceed the value specified by the manufacturer, typically 500µS/cm.
The performance characteristics of water cooled capacitors are significantly dependent on the stability of the cooling water supply system. A stoppage in the supply of the cooling water can cause a component to fail. Use of control and alarm systems helps to ensure that failures in the water supply system do not go unnoticed. Thermostats are used to ensure that capacitors are protected against over-heating in case of a failure in the water supply system. In addition, suitable protection devices are required to protect capacitors against overvoltages and overcurrents.
Water cooled capacitors are cheaper and occupy less space as compared to using banks of small capacitors. They are also more effective as compared to forced-air cooled capacitors. These capacitors are a suitable choice for applications where forced-air cooling systems cannot be used.
Water cooled capacitors are suitable for use in a broad spectrum of high power RF applications including welding, induction heating, and dielectric heating systems.
Source: Capacitor Faks blog
by Anthony Kenny
- Miniature RF Connectors for high-performance testing - April 24, 2025
- Space-Grade components available for immediate delivery - April 10, 2025
- Managing EEE components for LEO and lower cost space missions - December 17, 2024
0 comments on The anatomy of a water cooled capacitor