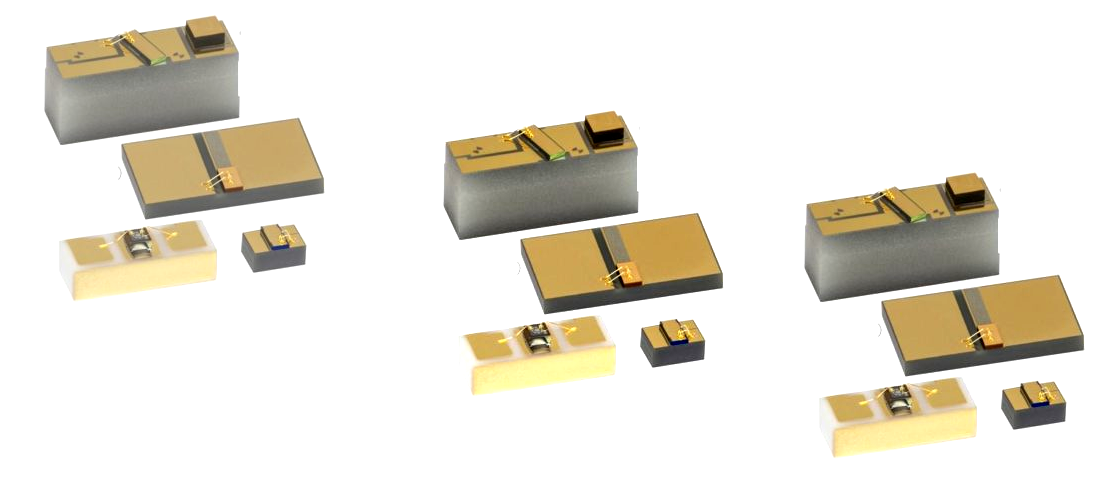
Silicon as a capacitor dielectric
- Posted by doEEEt Media Group
- On November 8, 2020
- 0
Capacitor blog examines the pros and cons of this dielectric material
Introduction
Capacitors are used in electronics circuits for a broad spectrum of applications including storing electric charge, delaying voltage changes, making resonant circuits, and filtering out unwanted signals. The type of dielectric material used is one of the key factors that determine the characteristics and applications of a capacitor. Other factors that influence the characteristics and applications of a capacitor include the packaging and the structure of the plates. The most common dielectric materials include aluminum & tantalum oxide, ceramic, plastic film, polymer, glass, mica, and paper.
Aluminum or tantalum plate capacitors with an oxide dielectric material are widely used for applications that require high capacitance. These electrolytic capacitors have high instability, poor tolerances, and their performance deteriorates when they are subjected to high leakage current or high temperatures. Plastic film and paper capacitors are usually used in circuits that demand capacitors with good aging performance, high stability, and high current carrying capability. For high-frequency applications, ceramic capacitors are a good option. However, these capacitors have poor aging performance. Mica and glass capacitors are suitable for applications that demand extremely high stability, reliability, and tolerance to high voltages and temperatures. However, these capacitors are typically expensive and are, therefore, not commonly used in low-cost devices.
Silicon-based dielectrics such as silicon dioxide and silicon nitride are commonly used in high-density capacitors. Capacitors with silicon dielectrics are ideal for applications that demand high stability, reliability, and tolerance to high temperatures. The performance characteristics of these capacitors make them a suitable choice for use in harsh environment applications. The following are the key strengths and limitations of silicon-based dielectrics.
Strengths of silicon-based dielectrics
High stability at high temperature
The performance of most capacitors is significantly affected by exposure to high temperature. Silicon capacitors are available in different temperature ratings, usually up to 250oC. High temperature silicon capacitors are suitable for a broad range of harsh environment applications including aircraft engine controls, avionics systems, automotive systems, downhole oil exploration systems, military applications, and so on. In addition, silicon capacitors offer highly stable capacitance performance as a function of voltage and temperature. Although the maximum capacitance of silicon capacitors is limited, they do not suffer ageing of capacitance. Moreover, unlike X7R and X8R capacitors, the reliability and capacitance of silicon capacitors are not degraded under DC bias conditions.
High potential for miniaturisation
Silicon-based dielectrics are commonly used in the fabrication of high density electronic devices. High-density silicon capacitors are usually fabricated in ultra-deep trenches, and they have very low leakage current and low loss factor. Passive integration connective substrate (PICS) is the most common technology for implementing high-density capacitors. This process allows the implementation of multi-chip modules (MCMs) and chip on board (COB), and it helps to realize smaller components with low power consumption. In addition, this process allows the integration of many basic functions into a single product, thereby helping to cut manufacturing costs. By employing the latest technologies, high volumetric efficiencies have been achieved. It is expected that the volumetric efficiency of silicon capacitors will continue to improve as the demand for high performance and miniaturized components continues to grow. So far, silicon capacitors with layers that are thinner than those of multilayer ceramic capacitor (MLCC) technology have been achieved.
Leakage current stability at high temperature
Leakage current is one of the capacitor parameters that can be affected when a capacitor is subjected to high temperatures. The dielectric material is the key factor that determines the leakage current of a capacitor. Over stressing the dielectric material can significantly increase the leakage current. The charging voltage and the thickness of the dielectric also have a slight effect on the leakage current of a capacitor. As compared to most high-temperature capacitors in the market, silicon capacitors have impressive leakage current-temperature characteristics. In addition, silicon-based dielectrics offer impressive insulation resistance that makes them an unmatched choice for coupling, blocking, and timing circuits.
Low failure rate
Capacitors find a wide range of applications in electronic circuits. As such, they are one of the most common passive components in electronic systems. The reliability of a capacitor is a factor of its failure rate. As compared to other passive components, capacitors have a higher rate of failure. Some of the key factors that determine the failure rate of a capacitor include operating time and loading conditions. Comparative reliability tests have shown that high-temperature silicon capacitors have better FIT (failure in time) rates as compared to high-temperature X8R capacitors.
Limitations of silicon-based dielectrics
Limited maximum capacitance
Although silicon capacitors have impressive characteristics including high stability at high temperature, very low leakage current, high insulation resistance, and high capacitance density, there is a limit to the maximum capacitance that can be achieved. It is expected that the latest advancements in technology will help to overcome this technological limitation. In addition to improving the fabrication process, manufacturers are exploring alternative dielectrics as a solution to the major technical barriers associated with silicon-based dielectrics.
Charge leakage
SiO2 is commonly used in the fabrication of capacitors for microelectronics devices. These capacitors are constructed by oxidizing silicon and using the oxide as the dielectric material. Since capacitance is directly proportional to the area of the dielectric material and inversely proportional to the thickness of the dielectric, manufacturers of electronic devices have been decreasing the area and thickness of the dielectric material to obtain miniaturized and high-density devices. As the thickness of the SiO2 dielectric film is decreased, the charge leakage through the dielectric material increases. Beyond a certain limit, it becomes difficult for the capacitor to store charge due to the leakage problem. Although DRAM manufacturers are using deep trenches to overcome leakage problem, the dielectric thickness limitation is a major barrier to miniaturization of microelectronic devices. Apart from improving the implementation process, manufacturers are also exploring alternative dielectrics to overcome this limitation.
Source: Capacitor Faks blog
- Space-Grade components available for immediate delivery - April 10, 2025
- Exclusive stock on doEEEt: How to access and request - April 10, 2025
- Managing EEE components for LEO and lower cost space missions - December 17, 2024
0 comments on Silicon as a capacitor dielectric