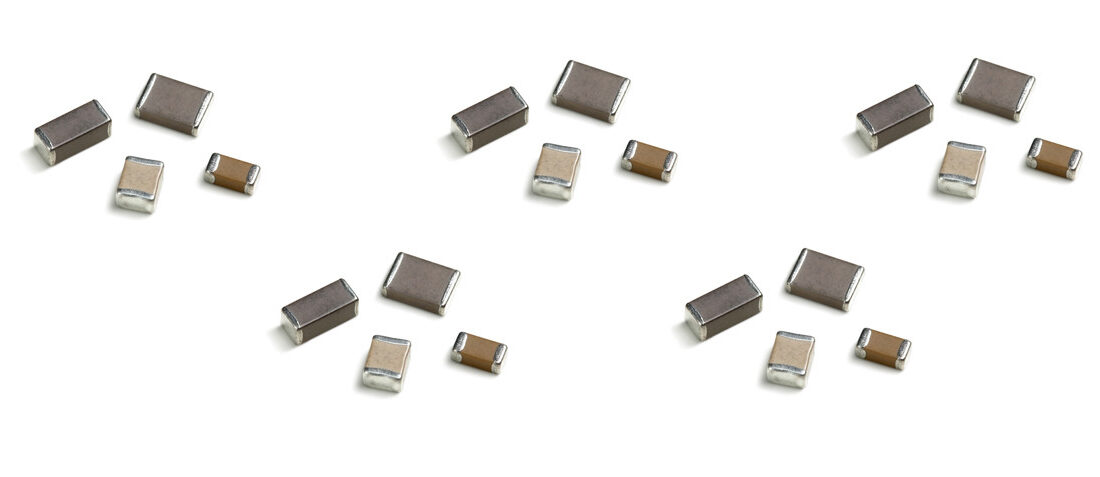
Performance, reliability and limitations of BME tech
- Posted by doEEEt Media Group
- On November 8, 2020
- 0
Today’s electronic devices are smaller in size and have more functionality compared to their predecessors. They are expected to get even smaller with the current advancements in manufacturing technologies. The trend towards miniaturization of components is mainly accelerated by better understanding of materials and improved processing techniques. Critical applications such as implantable medical devices and aerospace devices demand high reliability components. Therefore, even as components get smaller, they are expected to offer long-term reliability and better functionality.
The growing demand for smaller electronic devices that deliver higher performance and consume low electric power has played a key role in accelerating the technologies used in the manufacturing of passive and active components. Components that consume considerable amount of power and require more space on circuit boards are increasingly being replaced with low power miniature components.
Compared to single layer capacitors, multilayer ceramic capacitors offer higher reliability and better high-frequency characteristics. Furthermore, high capacitance multilayer ceramic capacitors are usually smaller in size compared to high capacitance single layer components. The use of multilayer ceramic capacitors in mobile electronic devices such as smartphones, tablets, and computers has increased the global shipment of these components exponentially.
Performance and Reliability of Base Metal Electrode Capacitors
MLC capacitors are widely used in various applications including automotive, telecoms, medical, military, and aerospace applications. Nevertheless, some applications such as aerospace and military systems demand higher reliability components. Capacitors for such critical applications are required to meet specified performance and reliability requirements.
The precious metal electrode (PME) technology and the base metal electrode (BME) technology are the most common technologies used for manufacturing capacitors. Traditionally, PME technology was the primary method of manufacturing capacitors. This technology uses combinations of palladium and copper. Despite the high reliability of PME capacitors, most manufacturers have switched to BME technology. This technology is slightly over two decades old and uses nickel or copper. Most of today’s multilayer ceramic capacitors are manufactured using BME technology.
Although the switch from the older PME technology to the newer BME technology can be attributed to the high price of palladium, the considerable improvement in the reliability and performance of BME capacitors over the last two decades has played a significant role as well. Compared to their earlier counterparts, the quality of today’s BME components is far higher, both in reliability, performance, and cost.
The BME technology allows fabrication of capacitors with high capacitance and a broad voltage range. As such, BME capacitors are used for a wide range of applications, ranging from low voltage uses to high voltage applications. BME capacitors are available in packages that are smaller than those of PME capacitors, therefore making them a suitable choice for applications with space constraints. PME capacitors can be up to four times larger than BME devices, and, when their higher cost is included in the equation, this makes BME technology more often than not the economical and technological choice.
Manufacturers of multilayer ceramic capacitors have been advancing processing technology and materials formulation to enhance volumetric efficiency, improve reliability, accelerate miniaturization, and reduce cost of capacitors. These advancements in processing and formulation are expected to enhance the reliability of BME capacitors to levels that can make them suitable for use in harsher environments such as oil drilling, aerospace, and other critical applications.
National Aeronautics and Space Administration’s S-311-P-838 specification defines the requirements for capacitors for use in high reliability space applications. This specification defines various properties including reliability, base metal electrode, and ceramic dielectric. Recently, National Aeronautics and Space Administration (NASA) approved AVX Corporation’s base metal electrode X7R dielectric MLCCs for use in aerospace and military applications, while the Defence Logistics Agency (DLA) has recently accepted KEMET’s qualification of COG and BP BME dielectrics to MIL-PRF-32535 “M” and “T” levels.
Limitations of Base Metal Electrode Technology
Although the base metal electrode technology is currently dominating fabrication of MLCCs, there are concerns about the suitability of such components for applications that demand high reliability such as space applications. Most mission-critical applications require mature technology with proven reliability. With over 50 years of proven performance, precious metal electrode technology is widely used for manufacturing capacitors for critical applications. Despite the demand for miniaturization in some of the critical applications where PME capacitors are used, the need to meet the specified performance and reliability requirements limits the newer BME technology, although, as per above, advances are being made in this area.
Studies have shown that the increased capacity density in BME multilayer ceramic capacitors has resulted in a decrease in the usable life of the components. This means that high capacitance BME MLCCs have lower life reliability, thereby making them an unsuitable choice for critical applications. It is estimated that multilayer ceramic capacitors with very high capacitances have usable life of less than five years. This property can be attributed to the fabrication method used to increase the capacitance density of base metal electrode multilayer ceramic capacitors. As the thickness of the dielectric layer is reduced, the lifetime expectancy of the capacitor decreases.
Sintering is a critical process in the fabrication of both PME and BME multilayer ceramic capacitors. Whereas the process does not affect the PME capacitors, it can affect BME capacitors. For BME capacitors, the thermal process is carried out in an environment that meets specific requirements to prevent oxidation of the inner nickel electrodes. Although carrying out the sintering process in a reducing atmosphere helps to prevent oxidation, it reduces the insulation resistance of the BaTiO3 dielectric materials. Nevertheless, advancements in BME technology are helping to reduce the effects of sintering on the insulation resistance of dielectric materials.
doEEEt provides you the most complete and updated information about Hi-Rel EEE parts
source: Capacitor Faks blog
- Space-Grade components available for immediate delivery - April 10, 2025
- Exclusive stock on doEEEt: How to access and request - April 10, 2025
- Managing EEE components for LEO and lower cost space missions - December 17, 2024
0 comments on Performance, reliability and limitations of BME tech