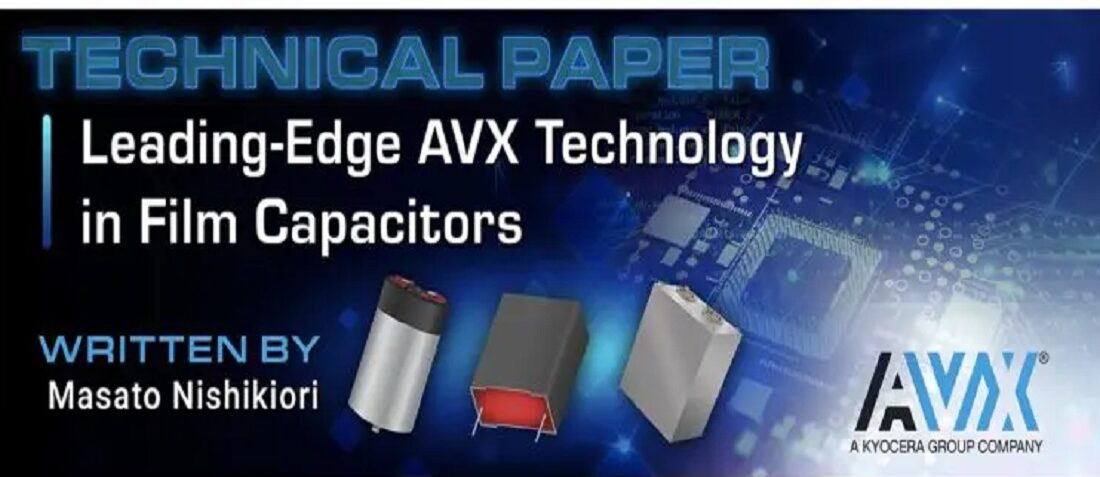
Leading-Edge Film Capacitors
- Posted by doEEEt Media Group
- On March 10, 2021
- 0
AVX Technical Paper
Leading-edge film capacitor technology available from AVX is described in Technical Paper written by Masato Nishikiori.
Introduction
With the advent of plastics in the middle of the 20th century, the film capacitor was introduced as a technological leap over traditional paper-based designs. Film capacitors use a thin plastic film as the dielectric that separates multiple metal electrodes. The electrodes are either deposited directly on the film (metallization) or are built from separate metal foils. The plastic metal sandwich is wound on a bobbin, and a terminal contact layer is deposited to connect all of the individual capacitor layers in parallel effectively.
Film capacitors can be divided into several families based on their application power requirements. On the low end of the spectrum, small surface mount chip capacitors are available in three common dielectrics: metalized Polyethylene Naphtalate (PEN), metalized Polyethylene Terephtalate (PET-HT), and metalized polyphenylene sulfide (PPS). These devices have become ubiquitous on PCB’s for a wide variety of functions, including decoupling, smoothing, filtering, and impedance matching.
A second family of film capacitors for medium power applications uses dry metalized polypropylene or polyester dielectric. It can be found in AC/DC filtering systems, high energy discharge circuits, and transient voltage protection.
Finally, high power film capacitors employ high purity oil impregnation to achieve superior energy density and a high voltage range of 1.2kV – 100kV, making them applicable in DC links, resonant filtering, and high voltage power supplies.
Standard Elementary Wound Bobbins
One of the primary drivers in advancing film capacitor technology is total component cost. A straightforward method for reducing cost, especially in medium and high power applications, is the standardization of elementary bobbins. The idea is to create a highly controlled, high yield, and cost-optimized family of wound capacitor bobbins that can be later connected in various shapes and sizes to build the final capacitor. As shown in the following figure, bobbin building blocks have been designed in cylindrical, puck, and flat shapes to be used individually or combined based on the final application.
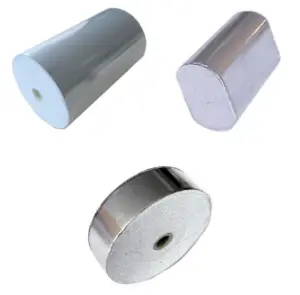
Figure 2: Standard cylindrical, puck, and flat bobbins
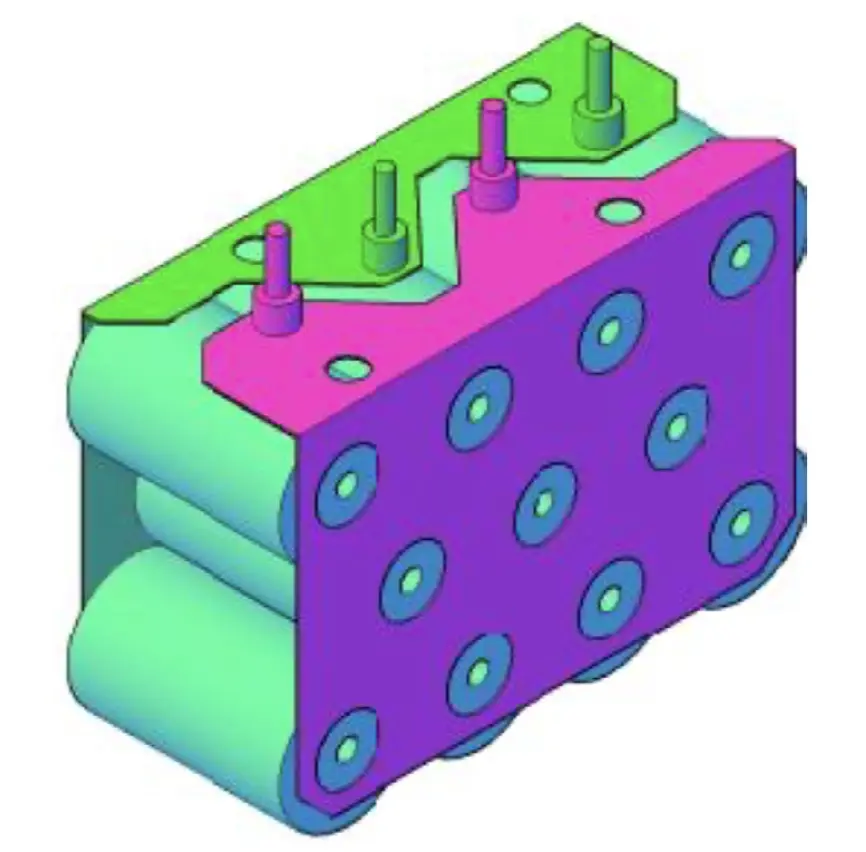
Figure 3: Cylindrical bobbins combined to make a high capacitance part.
Cylindrical designs are targeted at high capacitance applications, puck designs at high-current low-inductance applications, and flat designs when high I2t and low Rs are needed. An example is shown in Figure 3, where eleven cylindrical bobbins are connected in parallel to realize a high capacitance part.
The following table compares a standardized bobbin film capacitor to an equivalent electrolytic bank, and the advantages of the film capacitor are clear.
Controlled Self-Healing
Another primary driver in advancing film capacitor technology is physical component size. The reduction of physical size is constrained mainly by the thickness of the plastic dielectric. The plastic is thinned further and further. The electric field strength in the dielectric increases while simultaneously placing an additional burden on controlling layer integrity during manufacturing. The result is a higher propensity for defects and dielectric short circuits. To cope with this increase, self-healing mechanisms are used at several manufacturing processes to create high quality and extremely reliable capacitor.
As shown in the following figure, the self-healing process initiates with a weak point in the plastic film dielectric. This effectively creates a short circuit between the two metallization layers. The heat energy dissipated in this short circuit effectively demoralizes an area around the defect, preventing any further short circuit current.
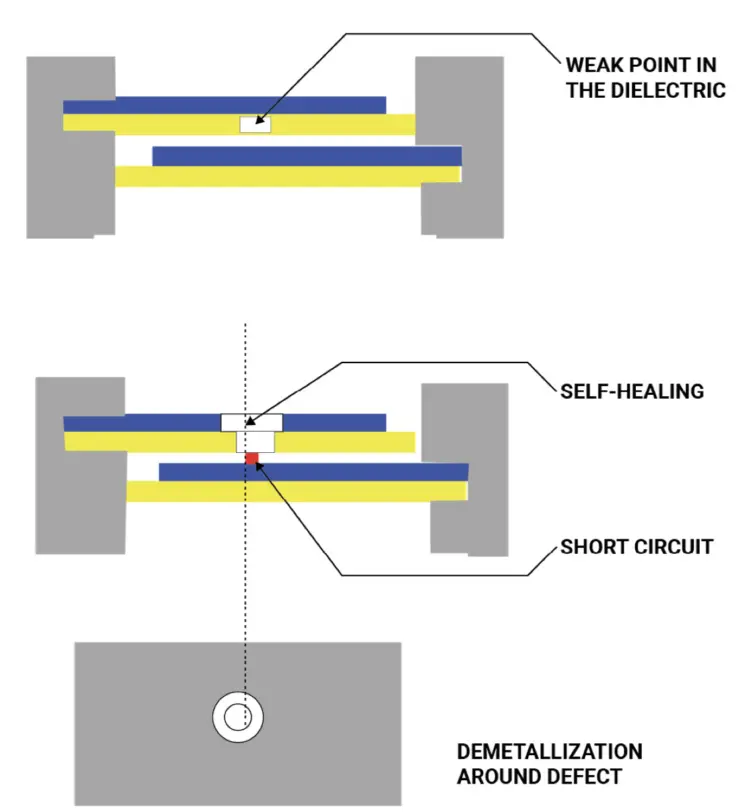
Figure 4: Depication of the basic low energy self- healing process
This self-healing process can be controlled during manufacturing using a specified voltage before winding, after winding, and after final assembly. Even during the product’s life, self-healing events occur in concise time durations and have negligible effects on the transient operation.
To minimize the demetallization area and limit the total overall capacitance effects, novel gate structures can be designed into the metallization layer, as shown in the figure below. Created with a laser or offset deposition process, these gates act as fuses to limit current flow above a certain threshold, thereby electrically disconnecting the affected defect area.
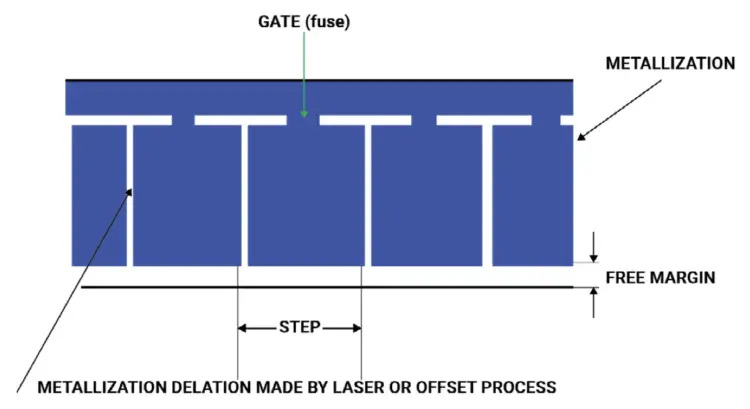
Figure 5: Gate segmentation for controlled self-healing
Unlike their electrolytic counterparts that exhibit catastrophic shorting failures at the end of life, film capacitors fail gracefully and slowly, accumulating self-healing operations and reducing effective capacitance. The metallization structure’s proprietary geometry achieves a balance between self-healing energy dissipation and reduction of volumetric capacitance efficiency. Decades of AVX experience in this area has resulted in miniaturized capacitors with extremely reliable lifetime performance.
Film impregnated metallized capacitors
For medium power discharge applications such as lasers, welding machines, and cable fault detectors, AVX offers film impregnated metalized capacitors. These devices use the aforementioned self-healing gate segmentation design in a metalized high crystallinity rough polypropylene construction. Impregnation with environmentally friendly rapeseed oil offers temperature performance, safety, and environmental stability. These capacitors are available in voltage ranges from 2kV to 75kV and energy characteristics of 150 kJ per can over a life of tens of millions of shots.
Oil-free wet technology
In high voltage, DC applications, such as DC filtering, AC-DC inverters, and solar/wind power generators, free oil is prohibited for safety reasons. AVX offers a film capacitor series using WET technology specifically designed for these types of applications. The capacitors are constructed from metalized high crystallinity smooth polypropylene using flat or cylindrical elementary bobbins. This high voltage range offers solutions for voltages from 1500V up to 3800V. The aforementioned controlled self-healing is essential to ensure safe and reliable behaviour and is achieved using a wet solution with both polypropylene metalized film and oil (without free oil).
Versatile AVX dielectric components
AVX produces a full range of film dielectric components – from low power SMD solutions for the commercial and automotive industry to medium and high power film capacitors suited to all power electronic applications over a voltage range spanning 75V volts up to 100 kV. Our technology includes both dry and oil-impregnated designs based on polyester and polypropylene dielectrics. Applications range from DC filtering, semiconductor protection, and tuning to discharge and high energy storage.
- Space-Grade components available for immediate delivery - April 10, 2025
- Exclusive stock on doEEEt: How to access and request - April 10, 2025
- Managing EEE components for LEO and lower cost space missions - December 17, 2024
0 comments on Leading-Edge Film Capacitors