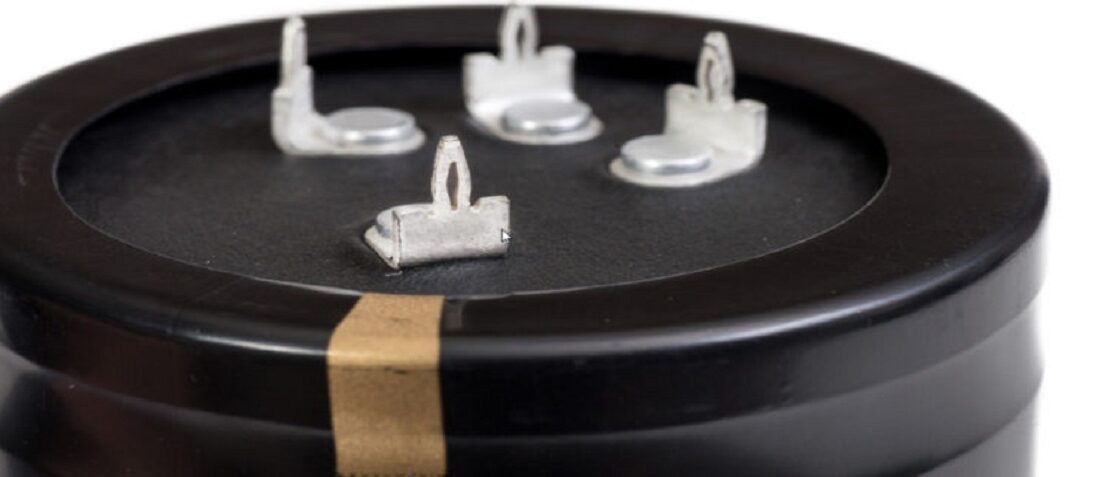
Introduction of Press-Fit Assembly on Aluminum Electrolytic Capacitors
- Posted by Kemet Electronic Corporation
- On May 26, 2020
- 0
Can Press-Fit capacitors still deliver the necessary robustness and electrical connection? Read a quick overview by Wilmer Companioni, Kemet Technical Marketing Team Leader.
It’s a simple concept, just press the pins into the holes and voila, you’ve installed your capacitor. On the face of it, it doesn’t sound like it is a very solid assembly, but we put a lot of thought into how we can bring the reliability you’re used to with our aluminium electrolytic Press-Fit capacitors. We’ll get into how this very simple method of assembly can still deliver the necessary robustness and electrical connection.
What is Press-Fit?
There are many ways to mount components onto aboard. The two most popular processes are surface mount technology and through-hole technology. Both of those processes use solder to mechanically affix components to the board.
One mounting technology type that has become increasingly popular is Press-Fit. This consists of “pins” that are capable of exerting lateral force on the holes in which they are inserted. Press-Fit has been successfully used in many electronics, such as IGBT modules for some time. KEMET is among the first to apply a Press-Fit connection to capacitors.
So, is it better than solder?
The question here is one that attempts to compare the mechanical robustness of solder-in connections with a press-fit connection. To take full advantage of a press-fit connection it requires laying down additional copper tracking around the connections and full plated through-hole.
The real question here is, “Is a press-fit connection is mechanically sound as a solder-in connection?” A bit of a loaded question if you ask me as the failure mode of a Press-Fit connection is slightly different than that of a solder-down connection.
Many times, large electrolytic capacitors are mechanically clamped to the casing because either solder-in or press-fit, such large components can create large amounts of torque on the board. Ultimately when equivalently affixed, solder-in connections and press-fit connections exhibit similar performance. The following is an example of a comparison of vibration performance.
An Option for Serviceability
Perhaps the biggest advantage of Press-Fit connections is that they can be more easily serviced. Our aluminium electrolytic capacitors are designed for long service life. Even so, sometimes these need to be serviced.
Using solder-in methods replacing a component can be a challenge. The equipment in which these components live are usually ones that must be continuously operational or there can be fines for down-time, such as power distribution systems. The less time the system is down the better. Replacing solder-in components may sometimes take hours but the replacement of press-fit items is more on the order of minutes.
Is Press-Fit Right for Me?
As with any good question, that depends. Press-Fit offers a favourable mix of serviceability with reliability. And that is the message of Press-Fit, being able to deliver a robust mechanical and electrical connection without sacrificing the necessary mechanical reliability of a system.
The only real way to know is to try out Press-Fit for yourself. While not a drop-in replacement for through-hole or snap-in connections, you can find you a necessary combination of capacitance, voltage, and size.
Check out Kemet offering of Press-Fit capacitors here.
- Decoding The DC-Link - June 8, 2022
- High Reliability: Tantalum Capacitors on the Front Lines of Defense - June 3, 2022
- One Turn Inductors Explained - March 24, 2022
0 comments on Introduction of Press-Fit Assembly on Aluminum Electrolytic Capacitors