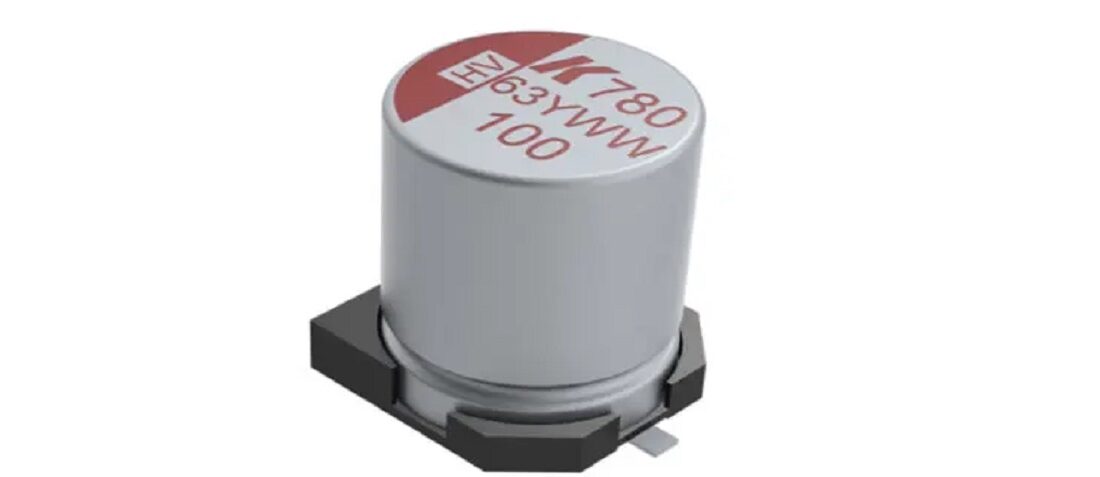
Hybrid Electrolytic Capacitors Bring High Ripple Current Capability
- Posted by doEEEt Media Group
- On June 23, 2021
- 0
Automotive Applications
The electrification trend in the automotive sector shows no signs of abating, and electrolytic capacitors have proved to be a reliable source of high-density power delivery in electric vehicles (EVs). The article published by EDN, authored by Jorge Vacas, product manager for electrolytics at KEMET Corp., explains use of hybrid aluminum polymer capacitors, in particular, it describes results of its application in a more efficient automotive design.
With every passing month, at least one carmaker announces a major development—be that an entirely new electric vehicle (EV) or an upgrade to an existing model. The latest research by analyst Markets and Markets indicates that the electrification sector is likely to expand at a compound annual growth rate of 11.9% to reach $129.6 billion by 2025 from $73.7 billion in 2020. This rapid increase reflects an incredible investment in research and development activity as EVs continue to win widespread consumer acceptance.
Technological progression does not take place in isolation, however. The supply chain exerts an enormous amount of effort in supporting the OEMs, with system and component specialists delivering innovative solutions across a broad range of areas.
Electrolytic capacitors have evolved to provide high-density power delivery with high cycle life and fast charge and discharge times in EVs. Hybrid aluminum polymer capacitors have emerged as highly-promising components for automotive applications with polymer and liquid electrolytic materials combined to deliver outstanding electrical performance for 48V architecture in mild hybrid electric vehicles (MHEVs).
The latest hybrid aluminum polymer capacitors most notably provide very high ripple current capability in a small package, which, when used in parallel for an existing 48V automotive inverter design, can reduce the number of required components, resulting in a more streamlined automotive design.
Importance of low equivalent series resistance
Let us take a deep dive into the design and performance characteristics of hybrid aluminum polymer capacitors and their use in automotive applications. Like traditional electrolytic capacitors, these devices comprise a wound structure of aluminum foil and paper in a metal can. The innovation comes with the electrolyte, which combines conventional wet liquids and modern conductive polymer (Figure 1). The polymer boosts conductivity and reduces equivalent series resistance (ESR), while the wet electrolyte maximizes contact surface area and increases voltage tolerance.
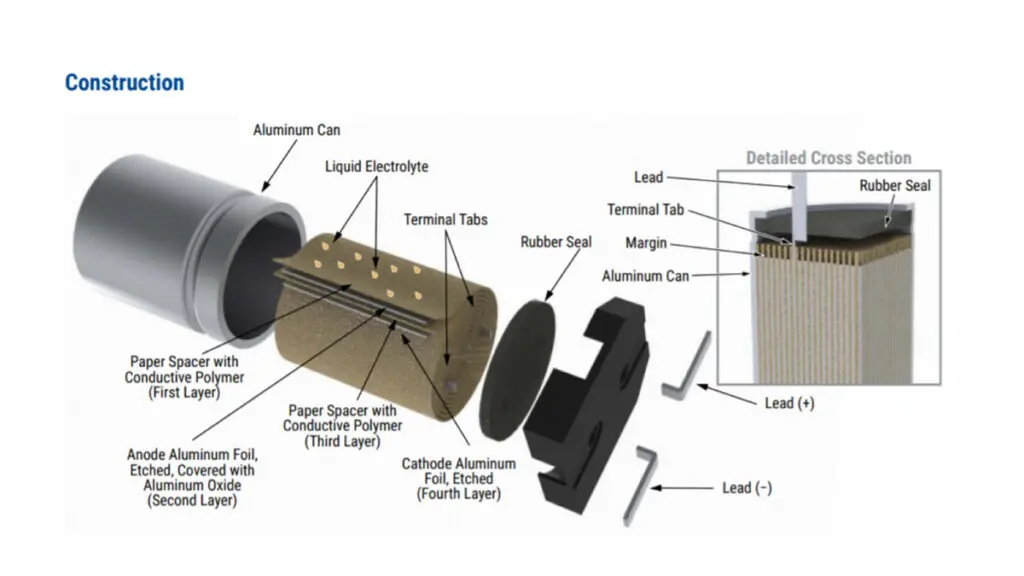
Figure 1 In hybrid aluminum polymer capacitor construction, the electrolyte combines conventional wet liquids with modern conductive polymer. Source: KEMET
The combination of these advanced materials and hybrid construction yields several game-changing benefits. For a start, ESR is a critical parameter because it directly affects the capacitor’s peak ripple capability along with its heat generation and temperature performance. Figure 2 demonstrates the exceptionally low series resistance for hybrids compared to traditional electrolytes across the entire frequency range.
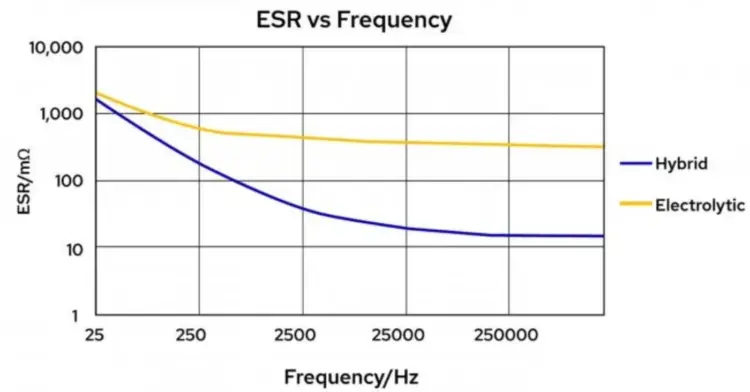
Figure 2 The ESR performance comparison of hybrid and traditional electrolytic capacitors shows the benefits of hybrid construction. Source: KEMET
When these capacitors are working at their ripple absorption limits, the hybrid design’s exceptionally-low ESR delivers a significant heat generation improvement. Transient simulations of high ripple currents show a temperature reduction of 20°C for the hybrid designs (Figure 3).
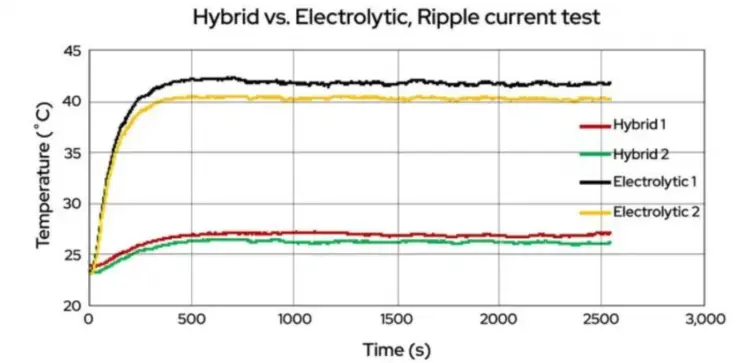
Figure 3 Ripple current temperature comparison of hybrid and traditional electrolytic capacitors shows a temperature reduction of 20°C for the hybrid designs. Source: KEMET
Specifically, in EVs, load variability and voltage regulation present engineers with significant design challenges. Onboard computers, engine control units, DC/DC converters, and 48V inverters require ripple stabilization and supply decoupling in harsh environmental conditions. Under high ripple conditions, the temperature performance makes hybrid aluminum capacitors ideal for applications where sensitive downstream electronics require properly smoothed and decoupled power supplies in harsh environments.
In addition to temperature performance, automotive applications also require high reliability to meet the AEC-Q200 standards. Under some circumstances, thermal shock can cause defects to the oxide layer inside a capacitor, leading to an excess of leakage current. However, hybrid polymer capacitors feature a soft self-healing mechanism with the presence of the liquid electrolyte, allowing electrochemical growth of the oxide. This process, which does not require a specific minimum current to be reached and can take place at relatively low local current density, allows for the smooth recovery of any imperfections. Consequently, leakage is stabilized and the reliability of the capacitor is assured.
When these robust mechanisms are combined with anti-vibration mounting structures, automotive qualification is comfortably met with rated lifetimes exceeding 3,000 hours, shock tolerance of 30 g, and operating temperature range from -55°C to 125°C. It is also worth noting that even though hybrid capacitors are more expensive than their traditional counterparts, their robust performance allows for much tighter rating margins and can result in price-competitive designs operating reliably at 90% of their rating.
Hybrid capacitor product development
Take the example of PHA225, an axial construction with a polarized all-welded design, tinned copper wire leads, and a negative pole connected to the case. The PHA225 winding is housed in a cylindrical aluminum can with a high purity aluminum lid and durable rubber gasket. The PHH225 hybrid capacitor, meanwhile, differs in that it contains a radial crown, which allows it to be mounted in a standing position.
Both PHA225 and PHH225 hybrid capacitors have a small size and high ripple current per unit volume, which are valuable attributes when designing for automotive and industrial applications. By using smaller, high-power-density hybrid aluminum capacitors in parallel for an existing 48V automotive inverter design, it becomes possible to reduce the number of required components and maintain high ripple current performance. Both capacitors are ideal for designing in high-power automotive applications, including DC-Link for 48V inverters, cooling fans, water pumps, power steering, and braking and injection systems.
Both of these components feature more than 3,000 hours of operation at +125°C, high-temperature capability of up to 140°C, up to 40 Arms, continuous load, and self-healing behaviors.
Then there is the A780 series, which represents KEMET’s first release of a surface mount (V-Chip) hybrid aluminum polymer capacitor (Figure 4). This capacitor series can withstand heavy vibrations (up to 30 g), meeting the stringent design requirements for automotive powertrain applications, including engine control units, DC/DC converters, 48V inverters for MHEV, switched-mode power supply, and computer voltage regulator modules.
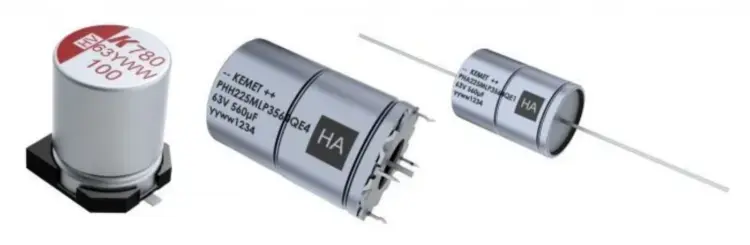
Figure 4 A780, PHA225, and PHH225 are AEC-Q200 qualified capacitors that combine highly-conductive polymer technology with liquid electrolytic material in a hybrid design. Source: KEMET
The launch of AEC-200 qualified capacitors, in addition to other products such as power inductors and electromagnetic compatibility solutions, illustrates a heavy investment in the automotive industry at a time when vehicle electrification continues to gather pace. Exciting times in the automotive industry!
- Miniature RF Connectors for high-performance testing - April 24, 2025
- Space-Grade components available for immediate delivery - April 10, 2025
- Managing EEE components for LEO and lower cost space missions - December 17, 2024
0 comments on Hybrid Electrolytic Capacitors Bring High Ripple Current Capability