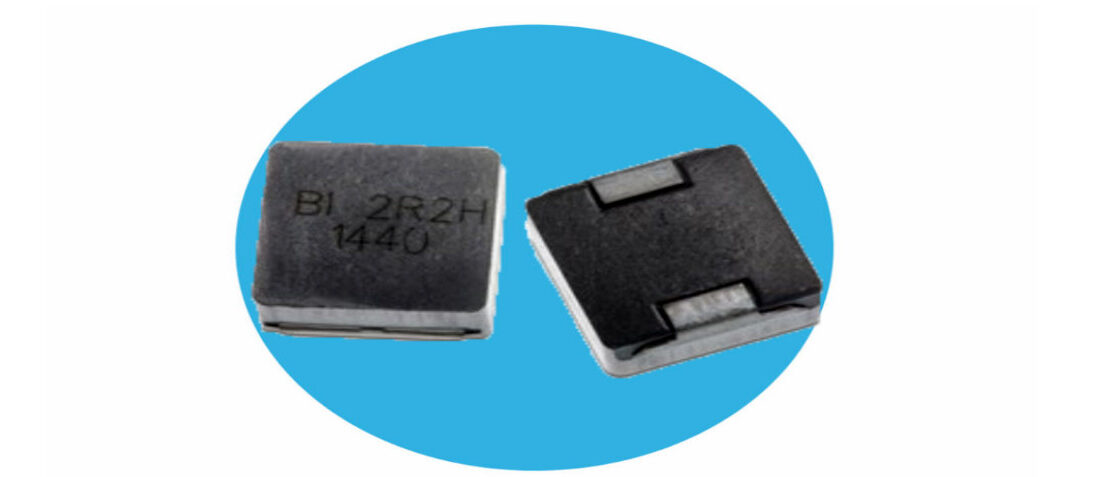
How to Choose the Right Inductor for DC-DC Buck Applications
- Posted by doEEEt Media Group
- On October 18, 2020
- 0
DC-DC converters of different varieties are widely used in markets such as telecommunications, automotive, medical (portable), and industrial. The ‘buck’ DC-DC converter is employed to step voltages down without isolation and utilizes an inductor as an energy storage element. This article will explain how to choose the correct inductor for optimum performance.
Choose the best option for your design using the comparation tool of doEEEt
Any kind of EEE parts requirement can be satisfied navigating in our database
Discover everything you can find in our database ⇒
A simplified buck converter schematic can be observed in Figure 1. The output voltage of this converter is always lower than the input voltage.
When S1 is open, the energy stored in the inductor sustains the current through the load through D1 with C1 also discharging into the load. S1 switches at high frequency and the duty cycle of switching defines the output voltage.
When S1 is closed, the DC input voltage is applied to the output filter inductor L1 and current flows through the inductor into the output capacitor C1 and to the load.
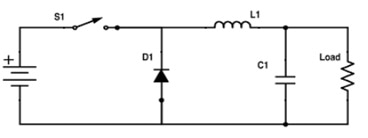
Figure 1. Simplified buck schematic
When selecting an inductor for a buck converter the following parameters need to be defined:
- Maximum input voltage = Vin max
- Minimum input voltage = Vin min
- Maximum output current = Iout max
- Operating frequency = f
- Output voltage = Vout
- Minimum output current = Iout min
So, for example, with f = 500 kHz, Vo = 5 volts, Iout max = 4 amps, Iout min = 0.5 amps, Vin max = 13.5 volts (car battery) and Vin min = 8.5 volts.
You can select what the inductor ripple current is – it sets output ripple voltage across the ESR of C1.
For this example, the inductor current stays continuous at the minimum specified load. So, the minimum of the ripple current just touches zero at minimum load, as seen in Figure 2. This makes control loop compensation a lot simpler. The inductor current stays continuous at any load, even with high ripple current, if D1 is a synchronous rectifier MOSFET. Though high ripple current does generate higher core losses.
Calculations
Since the operating frequency is 500 kHz,
Find the required inductance value, L
Find the delta current (ripple current), ∆I
Find the minimum duty ratio, Dmin
Find the peak current, I pk
Find the RMS current, I rms
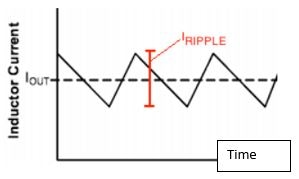
Figure 2. Typical inductor ripple current
An optimum inductor can be chosen using TT Electronics (TT) inductor datasheets. In this example, TT part number HA72L-06308R2LFTR is suggested, which is automotive grade, -55 ºC to +155 ºC (AEC-Q200 certified) with the electrical parameters below:
wdt_ID | TT p/n | L @ 0 amp | DCR typical | DCR max | I rms | I dc (sat) 30% Roll off | Typical picture |
---|---|---|---|---|---|---|---|
1 | HA72L-06308R2LFTR | 8.2 µH | 64 mΩ | 68 mΩ | 4.0 amps gives about 40 ºC Temp Rise | 7.5 amps | ![]() |
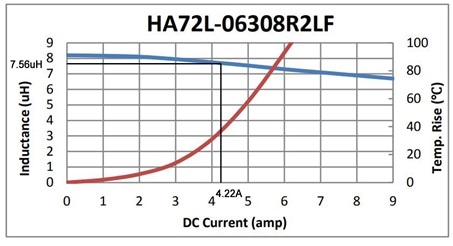
Figure 3. HA72L-06308R2LF DC bias and Temp rise
Figure 3 shows the inductance roll-off is 100 = 6.1% at 4.42 amps DC, which is close to the required value of 7.56 µH with a temperature rise of less than 40 °C.
The temperature rise in the datasheet graph is for DC current. In the example, there is also AC ripple current. A more precise temperature rise calculation, including ohmic and AC loss effects in the core and wire, is beyond the scope of this article but would be dependent on the below parameters:
- Skin depth at the operating frequency
- The surface area of the inductor
- Wire resistance at the operating temperature
- AC flux density, BAC, calculated from peak current, inductance, core cross-sectional area and number of turns
Source: AZO Sensors, TT Electronics article
This information has been sourced, reviewed and adapted by AZO Sensors from materials provided by TT Electronics.
featured image source: TT Electronics
- Space-Grade components available for immediate delivery - April 10, 2025
- Exclusive stock on doEEEt: How to access and request - April 10, 2025
- Managing EEE components for LEO and lower cost space missions - December 17, 2024
0 comments on How to Choose the Right Inductor for DC-DC Buck Applications