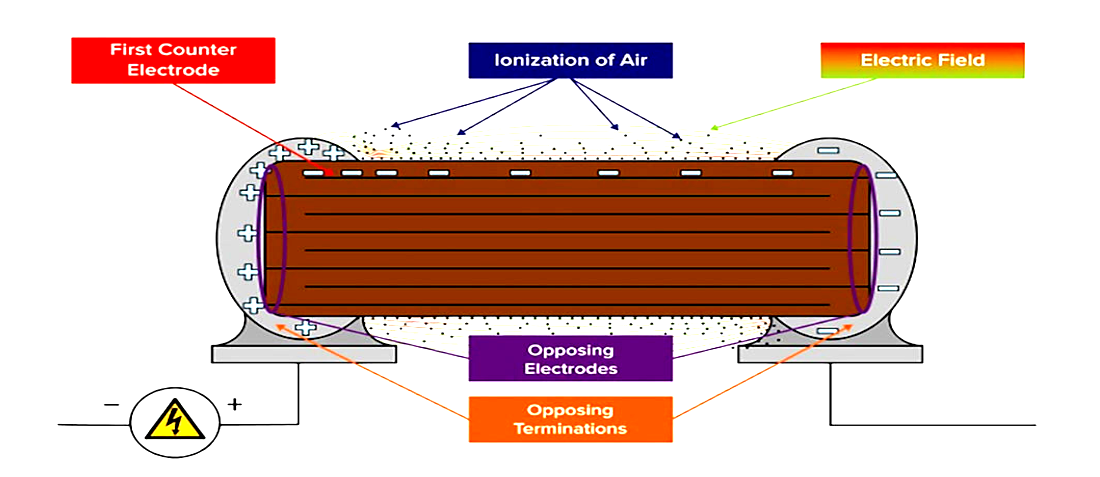
High Voltage MLCCs Arc-Over Prevention
- Posted by Kemet Electronic Corporation
- On December 17, 2020
- 0
In applications in which energy conservation is critical, such as wind or solar inverters or electric-vehicle (EV) powertrains, distributing power at high voltage can help to reduce I2R losses. The DC link supplying the inverter can be 3 V to 400 V in an EV application, for example, or even higher for wind or solar-power conditioning. However, high operating voltages like these bring additional safety challenges not only for end users but also for components — even those with a suitable voltage rating stamped on the case.
Let’s take a look at how multi-layer ceramic capacitors (MLCCs), which are often used for filtering, decoupling, or snubbing, can be affected by an applied bias of several hundred volts.
The accepted laws of physics tell us that a high MLCC voltage rating and the small package size are mutually incompatible: Increasing the voltage rating demands a thicker dielectric layer between plates, which, in turn, increases the size of the component. Even so, demand for small and lightweight power units require high capacitance and high voltage ratings within smaller and smaller package sizes. Designers of EV inverters or wind or solar microgenerators typically seek capacitors such as X7R type MLCCs in 0603 and 0805 case sizes, with voltage ratings of 500 V, 630 V, or 1,000 VDC.
Preventing arc-over damage and destruction
Component makers can go some way toward satisfying these demands with better-performing capacitor materials and construction techniques. In practice, however, factors such as creepage (the natural spreading of an electric field across a dielectric surface) and the tendency of a strong electric field to cause ionization of the surrounding air, as illustrated in Fig. 1, threaten the safety of components operated at high voltages.
When ionization occurs, if the applied voltage bias exceeds the inception voltage of the ionized air, a conductive path can form between device terminals or electrodes at different potentials, resulting in a corona discharge, or arcing.
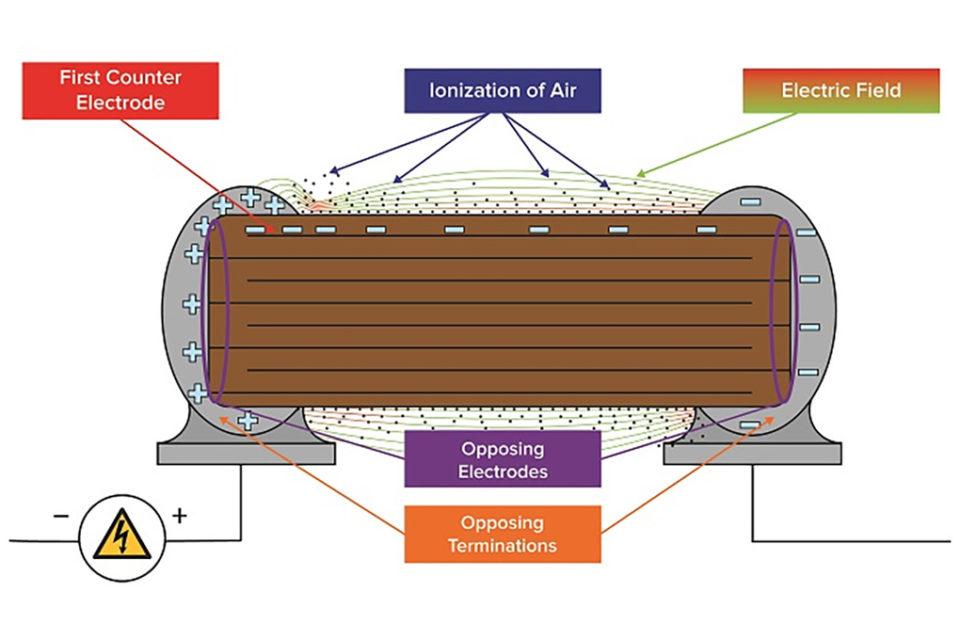
Featured Image Fig. 1: Ionization establishes conditions for terminal-terminal or terminal-electrode arcing.
The inception voltage at which arcing can occur is influenced by a variety of factors including atmospheric temperature and pressure, humidity, and termination creepage distance. The creepage distance, in turn, is affected by the presence of contaminants on the component surface, such as conductive dust particles or accumulated moisture. Ceramic materials that have high dielectric constant, such as X7R materials, have higher porosity — manifested as voids in the material surface — than other dielectrics, such as C0G. These voids tend to harbor moisture and dust, thereby making the component more vulnerable to arcing.
Arcing between terminals can be survivable, although repeated corona discharge across the surface of the device causes carbonized tracks to form and, over time, establish conductive paths. As discharges continue to occur, this will eventually result in short-circuit failure.
More immediately problematic is the possibility for discharge to occur between outer parts of the component and the first internal counter electrode sitting at the opposite potential, as depicted in Fig. 2. This usually causes a rapid dielectric breakdown, resulting in short-circuit failure; often accompanied by quite spectacular destruction of the capacitor.
Historically, capacitor manufacturers and materials specialists have developed various techniques to mitigate the causes of ionization and corona discharge. One of these is to coat the MLCC with a high-insulation polymer or glass-like coating to create a smooth and non-porous surface that provides a minimal opportunity for contaminants or moisture to accumulate.
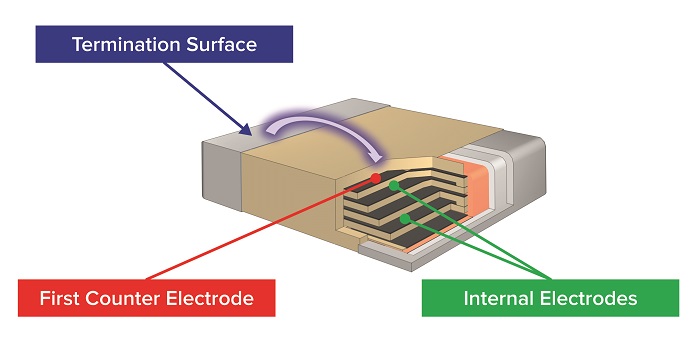
Fig. 2: Arcing between a terminal and first counter electrode usually causes rapid capacitor failure.
Although this technology has proven to be effective, there are several drawbacks, including the cost of the material and the additional process overheads to apply it. Moreover, the effectiveness of the coating can be compromised if the component body is not fully encapsulated or if the coating becomes damaged.
In addition, if the device is pre-coated, the board designer must ensure that the coating material is compatible with other materials used in the assembly. On the other hand, if the coating is applied after assembly, care must be taken to ensure that there are no voids or gaps, such as in the areas underneath components. These compromise the integrity of the coating and can allow the same arcing potential as an uncoated device.
Floating electrode
Alternatively, the capacitor’s ability to withstand a high applied electric field can be increased by adapting the internal structure.
One example is the cascading internal electrode design. Otherwise known as floating-electrode or serial-capacitor technology, this approach raises the voltage rating in the same way as connecting multiple capacitors in series and effectively increases the creepage distance, reducing the possibility of arcing when a high electric field strength is applied.
The floating-electrode design also provides effective mitigation of flex cracks by preventing a crack from crossing any pair of opposing electrodes and, thus, causing a short circuit. A flex-related crack may only cause a loss of capacitance or a safe open-circuit failure. One disadvantage is that the serial-capacitor approach reduces the effective capacitance, as would connecting discrete capacitors in series.
Internal shielding
A more recent development is to add a shield electrode inside the device, which sits at the same potential as the nearest terminal and extends toward the opposite terminal, as shown in Fig. 3. This can be imagined as being like a Faraday cage and allows a more conventional electrode layout compared to, say, the series-capacitor construction. Hence, the capacitance can be higher for a given voltage rating and device size. In addition, the shield electrode is compatible with flexible terminations to prevent stress cracking.
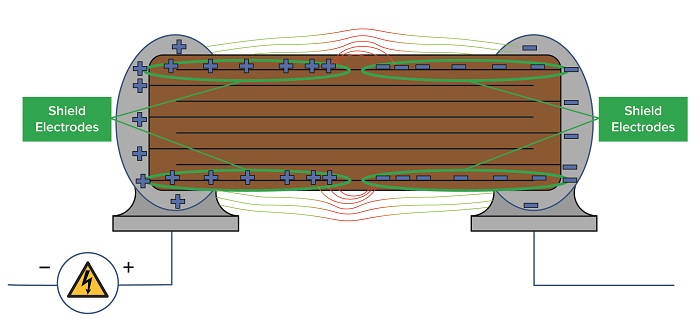
Fig. 3: The shield electrode reduces field strength in the region of the capacitor surface and first counter electrode.
When a high-voltage bias exceeding the inception voltage of ionized air around the capacitor is applied across the terminals, the presence of this shield electrode prevents corona discharge from causing a breakdown of the dielectric between the termination and first counter electrode, thereby protecting against the rapid short-circuit failure mode described in Fig. 2.
Because the shield electrode is at the same potential as the nearest terminal, the field concentration is localized in the shield electrodes rather than the termination surface and respective first counter electrode. This minimizes the difference in potential along the surface of the chip and increases the creepage-distance capability. As a result, even devices in small case sizes, or built with a high-porosity dielectric such as X7R, can benefit from increased immunity to arcing and the associated possibility of damage or device failure.
An example of a shield electrode design is KEMET’s ArcShield family of arc-resistant MLCCs that offer high voltage and high capacitance in small EIA-standard case sizes from 0603 to 1812 in commercial or AEC-Q200 automotive grades. Capacitance values range up to 0.33 µF at 500 Vdc, 0.15 µF at 630 Vdc, and 0.10 µF at 1,000 Vdc.
Conclusion
With the addition of a shield electrode, high-capacitance MLCCs up to 1,000 V in small chip-sized packages can resist arc-over discharge and greatly improve the reliability of high-voltage circuitry in applications such as EVs and renewable-energy generation. A shield electrode design delivers permanent protection and overcomes the drawbacks of conventional measures such as cascading electrodes or conformal coating.
- Decoding The DC-Link - June 8, 2022
- High Reliability: Tantalum Capacitors on the Front Lines of Defense - June 3, 2022
- One Turn Inductors Explained - March 24, 2022
0 comments on High Voltage MLCCs Arc-Over Prevention