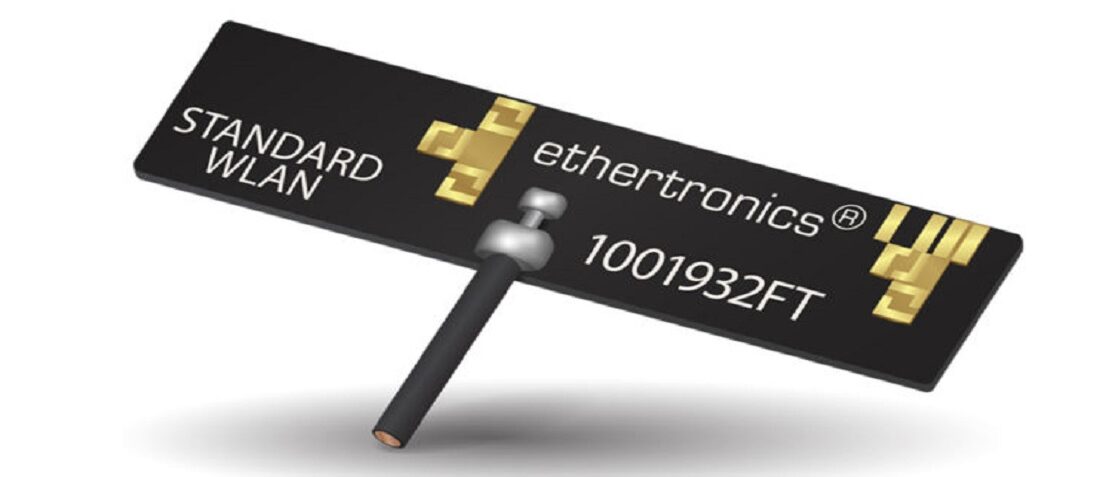
Best Practices & Advises for Antenna Tuning
- Posted by doEEEt Media Group
- On April 29, 2020
- 0
Connectivity is key in today’s world and devices in the market require strong signal strength to allow for peak performance. Integrating an antenna is not trivial, whether it is an off-the-shelf product or a highly customized solution, and should not be an afterthought. AVX Ethertronics white paper discusses antenna design considerations.
The AVX antenna design team strongly recommends considering the antenna design and/or the antenna integration process as early as possible, ideally during the product design and the radio module selection. A perfect match between the radio and the antenna will ensure all wireless connectivity needs are met.
Metal Impact
In most cases, the vicinity of metallic elements is not the best fit for an antenna, unless it is used as a reflector. Indeed metallic surface will reflect all the RF power from the antenna, and as antennas are reciprocal, it also affects the power/waves that try to reach the antenna. Metallic surfaces are the enemy of free space propagation and this is why an antenna inside a metallic box without any openings will not radiate any power outside this box. Even though in many cases, the antenna needs help from its ground plane to perform, the proximity of any metallic elements around the antenna is to be avoided. Such components are heat sink, connectors, mirrors, B2B connectors, shield cans, other PCB with ground, ferrite beads and coils, big capacitors, battery and its battery connector, LCD/Display and its wire harness, other cables or wires…
LCD and batteries are considered like metallic elements in the antenna world, as well as their wire harnesses connected to the main PCB of the device. The location and size of the battery or LCD connector/wire might impact the antenna tuning too. Indeed, as the antenna converts electric signals into electromagnetic airwaves, it induces RF currents running on the ground of the device including the battery/display and its connectors or wires. Having RF currents running on the battery or the LCD can create constructively (currents going in one direction, used as a ground plane extension) or destructive interference (currents operating in a zigzag shape). LCD is also an important source of electromagnetic noise and besides the impact on the radiation pattern, it can add noise on the signal, degrading the sensitivity of the device.
Cable Routing and Grounding
It is highly recommended to route cables and wires far away from the antenna location and if possible, ground those cables at few locations on the main ground of the device. This grounding can be operated by laser processing the cable jacket and by soldering small clips at that location down to the main grounding.
Antenna Coupling
The proximity of other antennas is impacting the RF performances, especially if the other antenna operates in the same frequency bandwidth. There are tricks to improve isolation or coupling between two antennas. Ethertronics’ IMD technology allows two antennas to be located closer. Though additional tricks can be used like slots in the grounding, reflector antennas added at specific locations, adding notch filters, making each antenna radiating with different polarization or making sure that the phase of each antenna signal is shifted by 90 degrees.
Cable Routing – Keep-out Area
Off-board antennas are antennas connected to the radio with a cable, connector or harnesses in some sort. Any pigtail accessory from the antenna needs to be routed properly in order to interfere constructively with the antenna radiations. On-board antennas might or not require a keep-out area or called clearance area. It is better to follow the recommended clearance area from the antenna datasheet to maximize the antenna performance. the keep-out area belongs to the tuning of the antenna as much as the antenna location and the dimensions of the PCB.
Interference with Printed Lines on the PCB
It is preferable to keep a big distance (quarter wavelength) between the antenna and high-speed digital lines. Those lines would act as antennas and would couple negatively the radiated RF power at a certain frequency, related to its equivalent quarter wavelength. Though it is possible to decouple those lines in order to reduce the coupling generated by using some inductors, which value varies between 80-150 nH, it is safer to keep those lines away.
Similarly, the DC lines feeding some motors, acoustic components like microphones, earpiece, speakers, vibrators can be dramatically impacting the RF performance of the antenna. Those lines can be decoupled up to a certain point with inductors placed on each line.
Impact from Materials
Any material surrounding the antenna with a permittivity (loosely called Dielectric constant, Dk, Loss tangent) different from 1 (air permittivity is 1, water is 80) will affect the antenna tuning. Other parameters such as the distance from those materials to the antenna and the amount will play a role in defining the equivalent effective permittivity surrounding the antenna. Any plastic resins, epoxy resins, potting materials, laminated structures will all have non-neglect-able RF losses applied to the radiation of the antenna.
Antenna Feed Line Design
An often taken for the granted parameter is the design of the transition between the output of the radio and the input of the antenna feed. That transition must present the proper expected impedance (often 50 Oms) in order to optimize the reflection coefficient at the antenna input level. In the event that the design requires a Z0 characteristics impedance, it is possible to ask the lamination manufacturer to add TDR coupons on its laminated panel to detect the lines that are off by more than +/- 10% compared to the expected value.
PI Network
To ensure that the impedance of the antenna will match the output impedance of the radio, it is a good practice to always add one PI shape matching circuit footprint (3 components, SHUNT-SERIAL-SHUNT) that can be used to define the matching circuit that will maximize the power transfer to the antenna. If the PI shape matching circuit is not used, then a 0 Ohm resistor is can be soldered on the SERIAL component footprint and the SHUNT components footprint can be left OPEN.
Matching Network Recommendations
When Selecting the components for the Matching circuit, filtering or decoupling, it is mandatory that the SRF (Self Resonance Frequency) of the chosen components are compatible with the frequency of the radio signal. SRF depends of the components size, packaging and manufacturing technology. We recommend using the Accu-P® and Accu-L® thin films Capacitors and Inductors in order to get the most precise matching circuit.
Testing Cable
During the design of the PCB, it is a good practice to consider the possibility of soldering a semi-rigid RF Cable to check the output of the RF radio or Antenna Impedance (for the debugging phase). To do that a non-assembled, three components T shape circuit SERIAL-SHUNT-SERIAL located before the antenna PI matching circuit (so the Matching circuit will be on the antenna and the soldered cable) is useful. The RF cable can be soldered on the SHUNT component footprint of the T-SHAPE and a 0 Ohm can be used to select the RF path either towards the radio or towards the antenna matching circuit.
Real Case Tuning Conditions
When designing an antenna for Wearable product or for a product that will be used in a very specific condition, always tune the antenna for these real user cases (when the device is worn or in the specific position) instead of tuning the antenna in Free Space conditions.
- Space-Grade components available for immediate delivery - April 10, 2025
- Managing EEE components for LEO and lower cost space missions - December 17, 2024
- Filtering Characteristics of Parallel-Connected Fixed Capacitors in LCC-HVDC - November 21, 2024
0 comments on Best Practices & Advises for Antenna Tuning