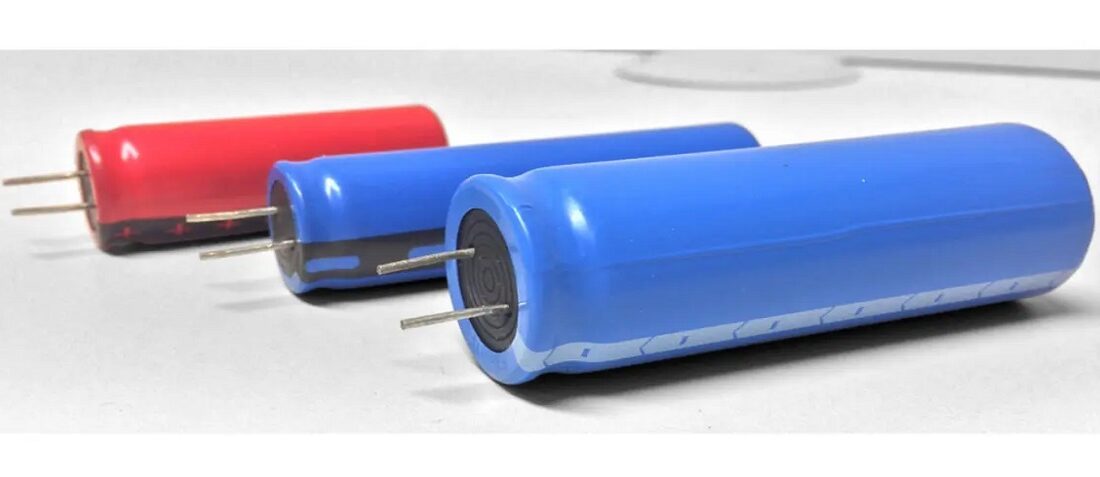
Anatomy of the New Supercapacitor Industry
- Posted by doEEEt Media Group
- On October 26, 2020
- 0
IDTechEx Releases new research report, “Supercapacitor Markets, Technology Roadmap, Opportunities 2021-2041”.
In 2010, there were no Chinese manufacturers in the top ten supercapacitor manufacturers. In 2020, 40% of them are Chinese. This has been achieved by world-class R&D, being in one of the largest markets globally, strong investment and government support including protective trading. However, China is not leading in capacitor-supercapacitor hybrids where the USA saw a $7 million follow on order recently.
Raghu Das, CEO of IDTechEx advises,
Supercapacitor manufacturers used to be divided into those making small ones for electronics and those that also made similar flat or cylindrical formats for electrical engineering such as the archetypal 2.7V 3000F cylinder. No longer. A considerable market for even large supercapacitors is rapidly emerging. The first big success with large ones is boxed car stop-starters at around 20Wh, with over five million sold. The number of auto makers going for that fit-and-forget, grab more electricity, waste less electricity proposition still increases. The natural extension of this logic is the newly committed adoption of larger supercapacitors for peak-shaving and acceleration boosting at 30-100Wh across the batteries in mild hybrid cars then full hybrid then totally replacing the lithium-ion battery if pure electric cars have not destroyed the hybrid car business by then.”
The new large versions appear in trains at 1kWh and 1MWh appears as hospital and data centre uninterruptable power supplies that double for peak shaving. It is a long way from small supercapacitors usually made to standards, easy to make and mostly commoditised at prices of 1 cent/F or less. IDTechEx counts 89% of supercapacitor manufacturers making them though Panasonic recently exited. 37% of these are in China because it exports them strongly, its share of the supercapacitor value demand being only 27% because of its giveaway pricing and lateness into car stop-start.
An exception to the commoditisation is small supercapacitors in the form of battery-supercapacitor hybrids BSH, aerospace and military ones working at 150C, capacitor-supercapacitor hybrids beating tantalum electrolytic on ripple and one fifth to one-tenth of the size and weight and ones in odd formats such as to go in a watch or smart card. Those working at 85C, -40C and 3V as single cells are less common and in demand.
Battery-supercapacitor hybrids (BSH) are almost always lithium-ion capacitors. They offer higher energy density often with effectively infinite cycle life and better charge retention than pure supercapacitors. Energy density several times that of pure EDLC supercapacitors. There is almost always confined to small units for electronics. IDTechEx measures that 24% of supercapacitor manufacturers now have a BSH range and of that 32% are made in China, where they are most successful commercially. China leads the world here, partly because they have so many large BSHs.
Several companies declare their supercapacitors to be “graphene” as a badge of honour. It can mean non-flammable, relatively non-toxic, no use of the volatile, toxic carcinogen acetonitrile, valuably improved series resistance, better voltage and energy density in a pure EDLC – all good things justifying a higher price.
Raghu Das adds,
IDTechEx measures that 8.75% of supercapacitor manufacturers now offer graphene versions, up from zero ten years ago. 43% of the manufacturers using graphene are in China so they are ahead in numbers, though certainly not in graphene supercapacitor research, much of which is aimed at the massive emerging market for replacing lithium-ion and lead-acid batteries with the highest energy density of 100Wh/kg or more. In research, this is usually achieved by boosted pseudocapacitance though some perfect the technology of the new commercial 100 Wh/kg lithium-ion supercapacitors. 33% of supercapacitor material research graphene-centric followed by carbon nanotubes then metal-organic frameworks.”
Large supercapacitors are more difficult to make, more profitable and represent the majority of the addressable market 2021-2041. Unlike small ones, they typically come with integral power electronics for optimal safe operation, microprocessors for an intelligent response, often cooling systems. 47.5% of supercapacitor manufacturers now claim to make them, up from few in the past. However, many of those are barely in the business, their web entries being more of a wish list that reality. 34% of these are in China – no dominance though it is coming up fast in this respect. This is assisted by the fact that a disproportionate amount of the demand for large supercapacitors is in China with the Government requesting that all parts of trains, buses etc. be made in China. On the other hand, China is badly behind in researching supercapacitor bodywork, smart skin and other radical advances scoped in the IDTechEx Research report, “Supercapacitor Materials and Formats 2020-2040”.
Raghu Das predicts,
Acquisitions and mergers will continue. One billion dollar supercapacitor businesses may be created by 2045. If the addressable markets we have analysed are strongly penetrated, then it will be much earlier. Given past disappointments, our upside forecast currently stands at $7 billion in 2041.”
- Managing EEE components for LEO and lower cost space missions - December 17, 2024
- Filtering Characteristics of Parallel-Connected Fixed Capacitors in LCC-HVDC - November 21, 2024
- ALTER SPACE TEST CENTER: testing approaches for New Space - September 30, 2024
0 comments on Anatomy of the New Supercapacitor Industry