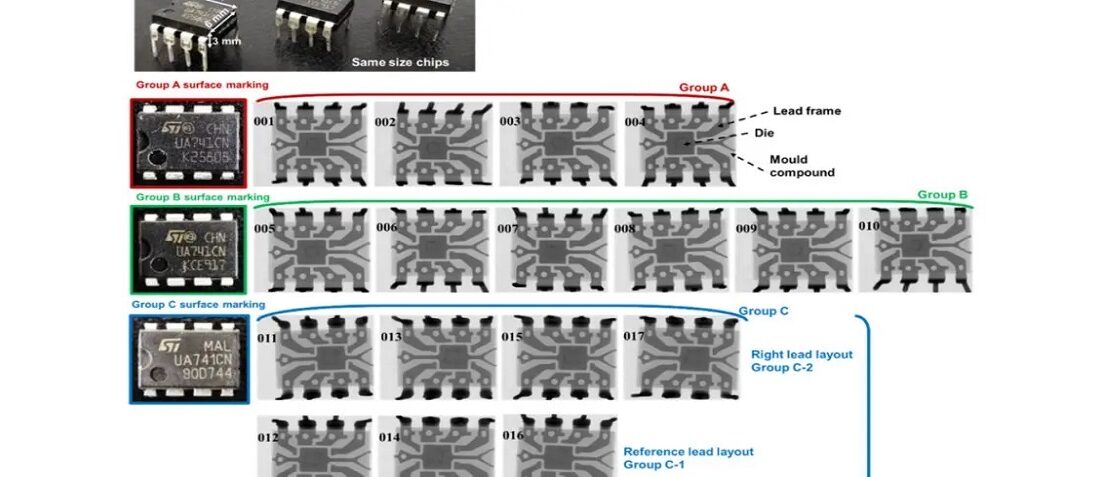
A Novel Non-Destructive Inspection Technique to Detect Counterfeit Electronic Components
- Posted by doEEEt Media Group
- On October 21, 2020
- 0
Using Thermography (NITECT)
Unverified or counterfeited electronic components pose a big threat globally because they could lead to the malfunction of safety-critical systems and reduced reliability of high-hazard assets. Researchers at Cranfield University in the UK propose a new fast, non-destructive method of electronic components inspection using pulsed thermography.
Introduction
The current inspection techniques are either expensive or slow, which becomes the bottleneck of large volume inspection. Therefore, as a complement to the existing inspection capabilities, a pulsed thermography-based screening technique is proposed in this paper using a digital twin methodology.
A FEM-based simulation unit is initially developed to simulate the internal structure of electronic components with deviations of multiple physical properties, informed by X-ray data, and thermal behavior under exposure to instantaneous heat. A dedicated physical inspection unit is then integrated to verify the simulation unit and further improve the simulation by considering various uncertainties caused by equipment and samples. Next, principal component analysis is used for feature extraction, and then a set of machine learning-based classifiers is employed for quantitative classification. Evaluation results of 17 chips from different sources successfully demonstrate the effectiveness of the proposed technique.
Among the diverse non-destructive testing (NDT) inspection methods, pulsed thermography (PT) – see Fig.1., is especially attractive for the inspection of UnVerified Electronic Components (UVECs) because it allows the inspection of a significant number of components simultaneously, facilitating a rapid and relatively low-cost inspection per part due to its rapid, non-contact inspection manner and its ability to produce intuitive inspection images.
Furthermore, a systematic investigation combined with a simulation-based approach can conveniently provide predictive insights into the PT detectability for the specific defect types in UVECs, thus remaining unascertained and scientifically worthwhile. This research addresses the challenge of identifying UVECs with physical defects, including the deviation of internal structures and material properties in the die, lead frame, and mould packaging, typically found in its supply chain. For instance, components with undersized die and over-simplified lead frame from disqualified manufacturing are reported to be short-lived and incapable of electronic option. Besides, unsourced, low-cost, and unqualified mould materials have been found in chips and have failed in long-term thermal fatigue cycles and aging tests. Therefore, it is essential to clarify the inspection feasibility, and which variability can be ascertained in PT thermography.
Counterfeit Inspection of Electronic Components
This research starts with an inspection of a common type of electronic chip: operational amplifiers (OpAmps). A total of 17 OpAmps were collected from various trade markets to investigate their thermal responses in PT.
All samples are common dual in-line package chips and are designed for the same electronic purpose (e.g., UA741CN). They have an almost identical external appearance except for surface markings. It should be noted that this study has no interest in investigating surface labeling. To reveal the internal structure of these chips, an X-ray inspection was adopted to obtain their lead frame and die details. Figure 2 (also featured image) presents the exterior dimensions, surface markings, and X-Ray images of 17 samples, categorized into three groups according to the surface markings.
Firstly, as shown by surface marking, chips of group A (from ‘001’ to ‘004’) and B (from ‘005’ to ‘010’) are from the same origin marked by “CHN,” but those of Group C (from ‘011’ to ‘017’) are original from “MAL.” The markings of “UA741CN” suggest the same electronic function. The ECs of Group B and C were tested by the electronic function testing and proven to be malfunctioning or broken, while others in Group A were verified as sound ones.
Secondly, all chips were tested using the same X-ray inspection, and the result of Group A is considered the ground truth of the internal structure. The internal structure of the lead frame and die in Group A and B are consistent, while those in Group C exhibit variations in the lead frame layout die position and size. For example, the die of ‘011’, ‘013’, ‘015’, and ‘017’ appear to the right half of the chip, while the die of ‘012’, ‘014’ ‘016’ are positioned towards the left.
Additionally, based on the intensity in X-Ray images, chips in Group C have different mould materials, which is a common variability between manufacturers. Based on these preliminary information sets, the simulation modeling and experimental inspection strategies are discussed below.
3D Modelling and Simulation
In this research, the electronic components are in a typical dual in-line packaged type composed of multiple layers composed of three primary materials: mold, lead frame, and die. To simulate the real structure of the EC, the X-ray images of verified chips are referenced to provide an accurate layout of the internal lead frame and die. According to the X-Ray images, the layout and dimension of the lead frame and die dimension are initially transferred to a binary mask. Then by mapping the mask onto the specific layers of the model, the real internal structure is simulated in the virtual environment. As a result, a 3D model is established with three layers with different materials, shown in Figure 3, including the mould compound layers, the lead frame layer, and the die layer.
To investigate the transient temperature transfer, the verified component model and variation models were established and simulated. Figure 4 presents the temperature distributions of the verified component model (shown in Figure 3) at 0.04, 0.08, 0.12, and 0.16 s after the flash.
See the full paper in the link below
- Space-Grade components available for immediate delivery - April 10, 2025
- Managing EEE components for LEO and lower cost space missions - December 17, 2024
- Filtering Characteristics of Parallel-Connected Fixed Capacitors in LCC-HVDC - November 21, 2024
0 comments on A Novel Non-Destructive Inspection Technique to Detect Counterfeit Electronic Components