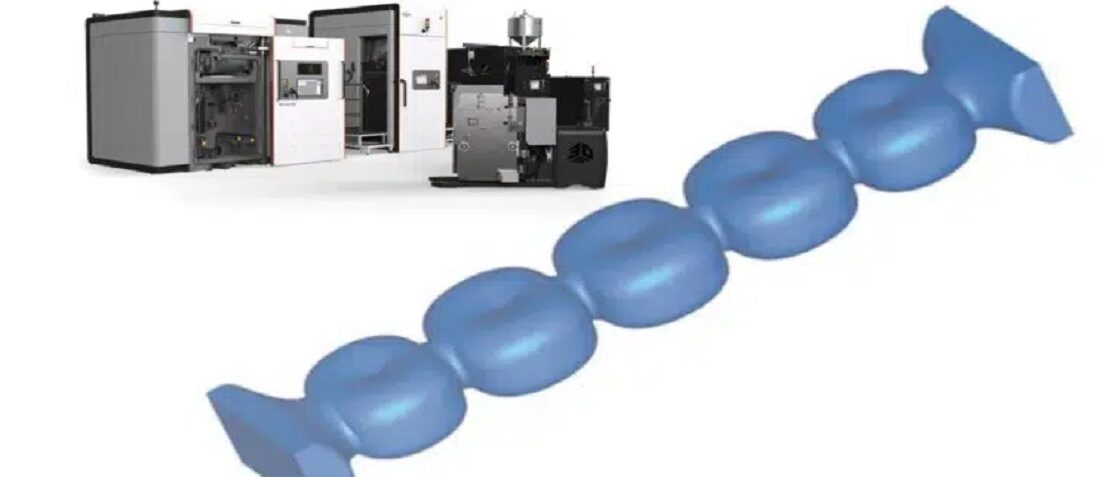
3D Systems to Deliver 3D Printed RF Components
- Posted by doEEEt Media Group
- On May 26, 2022
- 0
3D Systems & Airbus Defence and Space create novel 3D printed passive RF space components for the first fully reconfigurable satellite.
3D Systems announced Airbus Defence and Space had selected the company to produce critical components for its industry-first satellite innovation, OneSat. 3D Systems’ Application Innovation Group (AIG) has designed an end-to-end additive manufacturing solution – comprising materials, 3D printing technology, software, and applications expertise – to produce the components required for the large antenna array on these satellites.
Additively manufacturing these components offers design freedom to enable weight reduction, part performance optimization, and faster time to market, which aids in more rapid deployment of these unique satellites to meet end-user needs. 3D Systems was selected for this critical project based on the part quality achievable with its DMP systems and its demonstrated expertise and performance working with Airbus Defence and Space over the past seven years.
Previous collaborations include producing the first 3D printed radio frequency (RF) filter tested and validated for use in commercial telecommunications satellites and producing innovative switch assembly network designs for two Eurostar Neo spacecraft as part of the first large-scale deployment of RF products using direct metal printing.
Each OneSat satellite requires two large antenna arrays, one to transmit signals and one to receive. 3D Systems’ DMP Factory 500 Solution will be employed for serial production of the antennae components using LaserForm AlSi10Mg and specific parameters developed by the AIG for this application to achieve the required 30µm layer thickness. The DMP Factory 500 was selected for this project based on its build volume (500mm x 500mm x 500mm), accuracy, and rapid print speed. The intelligent multi-laser configuration of this printer enables the production of large seamless parts resulting in the highest surface quality with outstanding material properties.
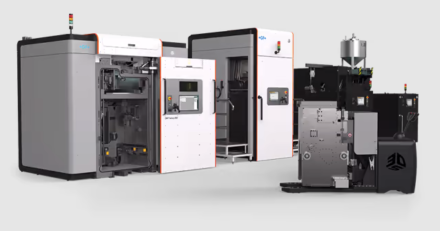
3D Systems’ AIG designed an end-to-end AM solution – comprising its DMP Factory 500, materials, software, and applications expertise – to deliver fully-qualified processes and components required for the large 3D printed antenna array and RF passive filters. source: 3D Systems
The printer includes a unique vacuum chamber that allows for the lowest possible oxygen (O2) content in the build chamber protecting chemical composition and reducing the moisture content of the metal powder alloys during manufacturing. This ensures optimum operating conditions for consistent part quality (e.g., mechanical properties and surface homogeneity), which is necessary for an industry with high quality and precision requirements. The DMP Factory 500 also includes 3DXpert®, which supports every step of the additive manufacturing workflow from design to post-processing, to quickly and efficiently transitioning from a 3D model to successfully printed parts.
In addition to providing design and production expertise, 3D Systems’ Application Innovation Group is also acting in the capacity of project manager. The company has identified subcontractors conducting post-processing and quality inspection, thus delivering a comprehensive end-to-end solution designed to help Airbus Defence and Space mitigate risk and reduce time to market. The AIG is also leading the technology transfer process, whereby they will enable another tier 1 supplier to ramp production of these fully-qualified components quickly. The supplier is also purchasing another DMP Factory 500 to complement its existing fleet and allow it to meet the quality levels required by Airbus.
“We value our long-standing partnership with Airbus Defence and Space and are pleased with how our collective work makes its mark in telecommunications satellites,” said Dr. Michael Shepard, vice president, aerospace & defense segment, 3D Systems. “As with our earliest work with Airbus on the first additively manufactured RF filter, we have the opportunity to bring another ‘first’ to the industry that is changing telecommunications. Our AIG has laid the groundwork for developing the application for this component and completing the technology transfer. We’re proud that 3D Systems’ technology can help Airbus lay the foundation for building a strong supply chain for serial production of passive RF hardware.”
“OneSat is a truly disruptive product. We wanted our design and manufacturing process to possess that same level of innovation,” said Stephen Phipps, OneSat antenna program manager, Airbus Defence, and Space. “Our company has a strong partnership with 3D Systems and has relied on its team of application engineers to help us bring our most advanced designs to life. Everything from the quality of the parts produced using their printers to parts qualification, quality management, and overall project management have helped Airbus Defence and Space maintain its position as an industry leader.”
Source: 3D Systems
- Space-Grade components available for immediate delivery - April 10, 2025
- Managing EEE components for LEO and lower cost space missions - December 17, 2024
- Filtering Characteristics of Parallel-Connected Fixed Capacitors in LCC-HVDC - November 21, 2024
0 comments on 3D Systems to Deliver 3D Printed RF Components