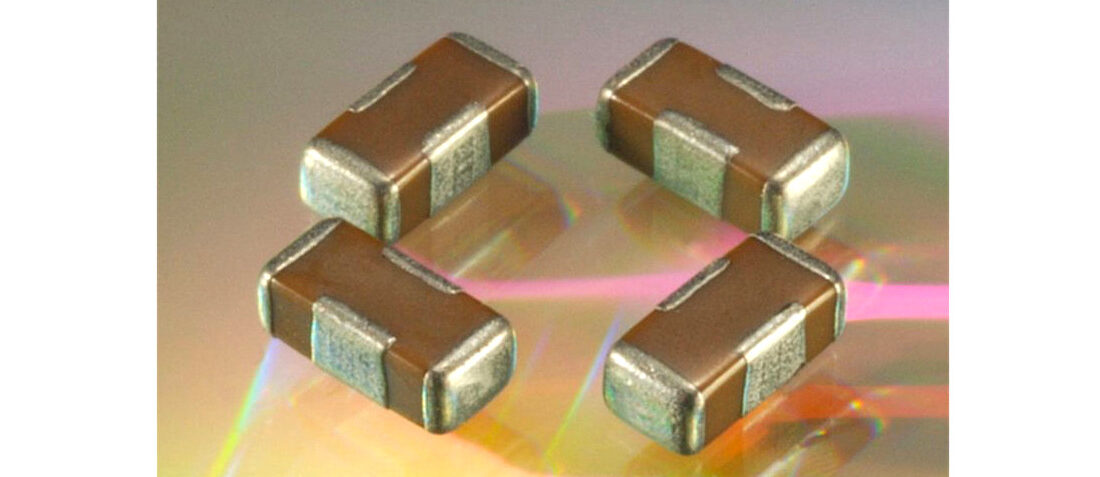
EMI Filter Cost Effective Solution for Brush DC Motor EMC Requirements
- Posted by doEEEt Media Group
- On March 9, 2021
- 0
Jeff Elliott from Electronic Design published an article with an explanation of EMI filter use and benefits to address increasing EMC requirements on brush DC motors.
Brush dc motors are inexpensive and easy to operate, providing a good balance of performance and price. As a result, billions are manufactured annually worldwide and used in such industries as automotive, aerospace, medical, appliances, and manufacturing, and billions more will be sold over the next 10 years.
However, increasing electromagnetic-compatibility (EMC) requirements, along with more crowded and “noisy” electronic environments, are threatening to drive the cost of these low-end motors to a level on par with more expensive brushless motors.
At issue is the electromagnetic interference (EMI) generated by the brushes rubbing against commutators, an inherent drawback of the design. To counteract the noise, a combination of shielding and filtering components is required. This not only drives up the cost but many EMI/RF filters for brush dc motors will not let them meet today’s higher EMC requirements.
“Many EMI filtering products do not filter out all forms of noise generated, and many cannot handle higher DC currents without a corresponding increase in their costs,” explains Christophe Cambrelin of Johanson Dielectrics, a company that manufactures a variety of multi-layer ceramic capacitors and EMI filters.
To address these concerns, passive component companies offer more advanced EMI filters that only slightly increase costs of brush dc motors while meeting the evolving EMC requirements.
Monolithic EMI filters provide significantly more RFI suppression for brush dc motors while rejecting a much wider frequency band. The EMI filter isn’t affected by the amount of dc current required.
Noisy Electronics
Electronic devices receiving strong electromagnetic waves often induce electric currents in the circuit and interfere with intended operations. EMI can even physically damage equipment. Making the problem worse, increases in operating circuit frequency expand the affected frequency range while miniaturization of electronic devices shrinks the distance between a noise source and affected circuits. If that wasn’t enough, many electronic devices are more sensitive to noise, even if it has less energy, because circuits today operate at lower voltages.
As a result, industries such as the automotive sector are increasingly turning to brushless dc motors. With these, the commutation is done electronically. Therefore, there’s significantly less noise generation (no noise generated by mechanical commutation), but the complexity and cost of implementation are increased.
So, given a choice, OEMs prefer the relatively low price of brush dc motors gave the quantities involved.
EMI Filtering
EMI/RFI interference is either radiated or conducted over a frequency range of between several hundred hertz to several gigahertz.
Radiated noise is generated by the voltage applied at varying levels to the wiring. To confine radiations in the motor housing, several precautions should be taken by manufacturers of brush dc motors. The most important is that the motor-housing material should be metal, and the housing should also have a metal cap. If the cap is plastic, users need to cover it with a shield of metal or metallized PCB.
When EMI/RFI is conducted, the noise generated travels along with the electrical power leads and is then radiated. Shielding is ineffectual against this conducted noise, so filtering with a separate device is required.
Traditional common-mode filtering includes low-pass filters comprised of capacitors that pass signals with a frequency lower than a selected cutoff frequency and attenuate signals with frequencies higher than the cutoff frequency. Options for OEMs are two-capacitor differential, three-capacitor (one X-cap and two Y-caps), feed-through filters, common-mode chokes, LC filters, and combinations of these.
To meet increasing EMC requirements, however, low-cost devices such as two-capacitor differential filters are insufficient because unmatched capacitors generate a different filtering of each line, and thus there’s mode conversion (i.e., part of the common-mode noise is transformed into differential-mode noise, and vice-versa). Traditional three-capacitor filters are adequate, provided the EMC requirements are only at relatively low frequencies (<150 MHz, such as AM/FM radios in cars).
Although three-capacitor filters provide good filtering, they are generally ineffective at filtering noise in telecom frequency bands. Other devices like feedthrough filters offer good rejection over a wide frequency band but become expensive when the power line must carry several amps of current. In addition, feedthrough filters are single-ended devices, and therefore may introduce mode conversions (like 2-cap filters).
“Regardless of the noise generated, if high dc current is required, you need a large, expensive feedthrough filter, which eliminates brush dc motors as a low-cost alternative,” says Cambrelin.
For brush dc motors, a possible alternative to the low-pass filter is a common-mode choke. When a common-mode signal (same ac current) travels through each winding of the common-mode choke, the magnetic field coming from each winding adds up, and the impedance, therefore, increases significantly. On the other hand, when a differential signal (opposite ac current) goes through each winding, the magnetic field coming from each winding subtracts from each other and impedance decreases significantly.
That’s why common-mode chokes block common-mode noise but let a differential signal go through. Similar to feedthrough filters, it takes a larger and more expensive common choke to carry a significant current (more than 1 A rms).
Despite the popularity of common-mode chokes, a better alternative may be monolithic EMI filters. Compared to common-mode chokes, monolithic EMI filters provide significantly more RFI suppression in a substantially smaller package. A monolithic EMI filter also rejects a much wider frequency band and isn’t affected by the amount of dc current required because it’s mounted in shunt (between lines and ground).
EMI filters combine two balanced shunt capacitors in a single package, with mutual inductance cancellation and shielding effect. These filters, use two separate electrical pathways within a single device attached to four external connections.
Like other EMI filters, monolithic EMI filters attenuate all energy above a specified cutoff frequency, only selecting to pass required signal energy while diverting unwanted noise to ground. The key, though, is the filter’s low inductance and matched impedance. With monolithic EMI filters, terminations connect internally to a common reference (shield) electrode and the plates are separated by the reference electrode.
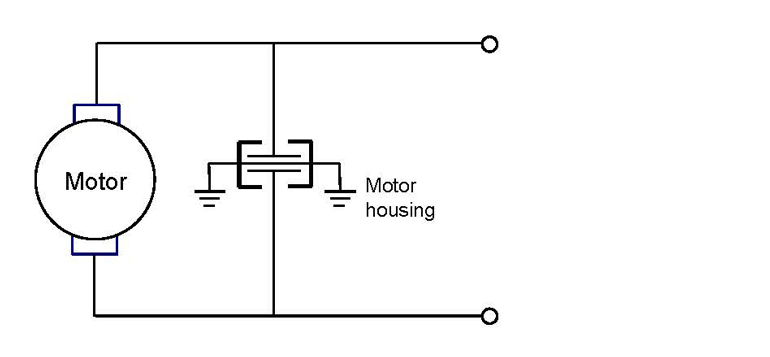
Monolithic EMI filters are effective from 50 kHz to 6 GHz and filter both common- and differential-mode noises. The filter also has virtually no limit to the amount of dc current because it works in parallel with the motor and no dc current flows through it.
Monolithic EMI filters can be effective from 50 kHz to 6 GHz and filter both common- and differential-mode noise. The filter also has virtually no limit on the amount of dc current because it works in parallel to the motor and no dc current flows through it.
PWM Signals
Regardless of the type of filter, an often-overlooked factor is the fact that many brush dc motors are controlled by pulse-width-modulated (PWM) signals, says Cambrelin. With PWM signals, the voltage is switched on and off quickly between a few kilohertz and tens of kilohertz. The total power supplied is based on the time the switch is on compared to the off periods.
PWM signals are particularly suited for motors because the motor’s time constant is very long compared to the period of a PWM signal. That’s why a brush dc motor acts as if the average of the PWM signals was applied on the power leads.
“When you first test the motor in the lab, the EMI filter may perform well, but everything changes when you apply PWM signals on the power leads,” explains Cambrelin. “You want to filter out the noise, but not unintentionally filter out the PWM signal. If you don’t choose the right filter, the motor may not even start.”
This can be a problem for users unfamiliar with developing differential LC filters.
With monolithic EMI filters, there’s no need for special skills in filtering. The filter’s response (i.e., rejection of common-mode noise vs. frequency) is provided directly by the manufacturer. Companies are also working on a device for brush dc motors that will let users mount the monolithic EMI filter on the housing without manufacturing a PCB.
“EMI issues are just going to become more of a problem with the higher frequencies with Bluetooth, Wi-Fi, and now 5G devices,” says Cambrelin. “That means EMI filters will have to handle wider frequency ranges while letting appropriate signals pass through. This will help OEMs meet regulatory standards in most countries that limit the amount of noise that can be emitted.”
featured image source: Johanson Dielectrics
- Managing EEE components for LEO and lower cost space missions - December 17, 2024
- Filtering Characteristics of Parallel-Connected Fixed Capacitors in LCC-HVDC - November 21, 2024
- ALTER SPACE TEST CENTER: testing approaches for New Space - September 30, 2024
0 comments on EMI Filter Cost Effective Solution for Brush DC Motor EMC Requirements