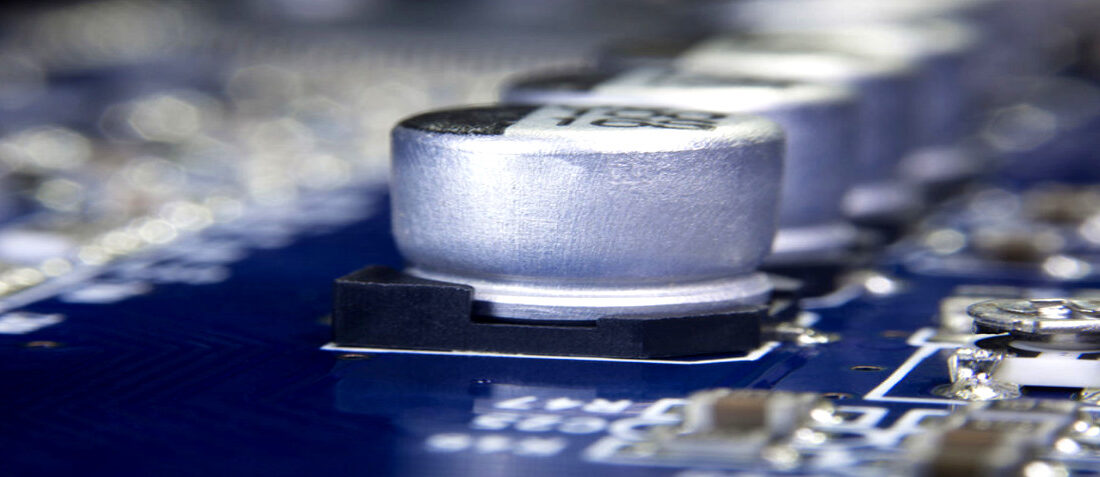
Electrolytic Capacitor: Best Practices for Increasing Profitability
- Posted by doEEEt Media Group
- On September 11, 2019
- 0
Aluminum electrolytic capacitors are among the most complex of all passive electronic components and requires multiple technological capabilities under one roof to produce. This includes the knowledge of chemically etching and forming anode and cathode foils (a very specialized process); the application and performance of electrolytes that include water, alcohol, and polymer-based materials (each granular disciplines within their own sub-category of electronics) as well as disperse materials requirements, such as separator papers, rubber stoppers, aluminum cans, tabs, and lead wires. In this ongoing article on Linked In, Paumanok IMR describes “best practices” that have increased profitability in the complex world of aluminum electrolytic capacitors.
Aluminum Capacitors: Highest Variable Costs in Foils
In multiple studies by Paumanok IMR between 1988 and 2019 on the subject of aluminum capacitors and the costs associated with their production, the following cost savings measures have proven to be most effective in increasing the profitability of aluminum electrolytic capacitor manufacturers.
Another item we have discovered over the years is that while production of aluminum electrolytic capacitors remains intact in Asia, Europe and the Americas, it has largely become an Asian only production business (With due note to the remaining vestiges of unique capabilities in South Carolina, USA and Heidenheim, Germany, the aluminum electrolytic capacitor business, and its unique supply chain- is largely consolidated in Japan, China and Malaysia today).
Aluminum capacitors, are electrolytic components, and are produced in a variety of configurations including radial leaded, axial leaded, vertical chip, snap-mount small can; large can screw terminal and organic polymer horizontal molded chip designs. Aluminum capacitors are almost exclusively wet designs, which mean they require an internal liquid electrolyte to operate. Some designs are solid- or dry type, and employ a conductive polymer instead of a liquid chemical electrolytic to achieve the desired voltage and equivalent series resistance required by the design engineer. Aluminum capacitors offer the design engineer a high capacitance, high voltage solution and a low comparable price.
One interesting factor about aluminum electrolytic capacitors is that they contain multiple types of raw materials in their construction, including etched anode and cathode foils, electrolytes, cans, tabs, lead wire or terminals, rubber stoppers and foot-pads. Here is a summary of methods by which aluminum electrolytic capacitor manufacturers have reduced their respective cost structures and increased profitability over the years.
In-House Foil Forming and Etching:
Many of the top vendors of aluminum capacitors can etch their own anode and cathode foils as a way to cut costs. In-house etching of anode and cathode foils requires chemical expertise and low-cost energy as etching and formation are technically demanding, “electricity intensive” practices. There is movement in the industry to etched and form foil in extremely low energy cost nations and this process is also designed to decrease costs because electricity consumption is a key cost factor in forming capacitor foil.
Low Cost Regional Production:
Another method of cost-savings employed by global manufacturers of aluminum capacitors includes the intentional production of large volumes of radial leaded and vertical chip aluminum capacitors in low-cost production regions of the world (especially in China and Malaysia).
Massive Economies of Scale:
Global aluminum electrolytic capacitor production is dominated by only four players and they are all Japanese producers. This has remained unchanged for at least 31 years. One method that they employ to achieve better costs with all raw material vendors is massive economies of scale (@20-25 BB Pieces per year). This gives each manufacturer massive buying power when it comes to feedstock materials such as Bauxite, or high purity aluminum sheet; or chemical precursors for chemical electrolytes; rubber materials for stoppers, or specialty lids and sealers for aluminum cans.
Source: Paumanok article
- Managing EEE components for LEO and lower cost space missions - December 17, 2024
- Filtering Characteristics of Parallel-Connected Fixed Capacitors in LCC-HVDC - November 21, 2024
- ALTER SPACE TEST CENTER: testing approaches for New Space - September 30, 2024
0 comments on Electrolytic Capacitor: Best Practices for Increasing Profitability