HYPERBOLOID CONTACTS
- Posted by IEH Corporation
- On August 5, 2019
- 0
The HYPERBOLOID contact is an advanced design that satisfies performance requirements previously considered impossible. Radically different in concept, it is used in connectors having the highest standards of performance. The distinguishing feature of the HYPERBOLOID socket is the hyperboloid-shaped sleeve formed by straight wires strung at an angle to the longitudinal axis. Viewed from the side, you see a curve defined by a series of apparent short straight-line segments which are tangent lines to points along a hyperbolic curve. This geometry provides for a design which has a decreasing circumscribed circle when viewed from the entry. It begins larger than the pin acceptance diameter and is less than this same diameter at the center. When the pin is inserted into this sleeve, the wires stretch, well within elastic limits, to accommodate it. In so doing, the wires wrap themselves around the pin providing a number of continuous line contact paths. The illustration below will assist in visualization.
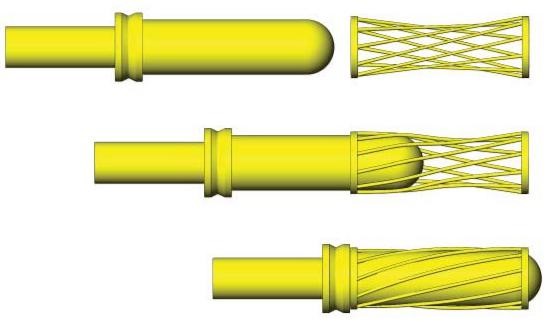
The actual physical construction of the contact involves several components. The wires are strung on an internal wire carrier (inner sleeve) which is subsequently capped or enclosed by a front outer ring (front sleeve) and rear ring which includes the termination configuration (terminal). All components to the assembly are completely finished with the specified electroplating prior to assembly. The wires are continuous process plated on reel before use. In this manner, interface finish requirements can be controlled very closely without the common problems of gradient, shadow, or other finish imperfections often appearing in alternative designs. Very often, this processing feature permits the specifier to reduce precious metal content with resultant savings. Joints are calculated interference fits, insuring gas tight interfaces between all elements of the HYPERBOLOID construction. An exploded view is provided next.
The unique geometry, precision processing, and careful attention to quality result in a highly desirable contact design which provides:
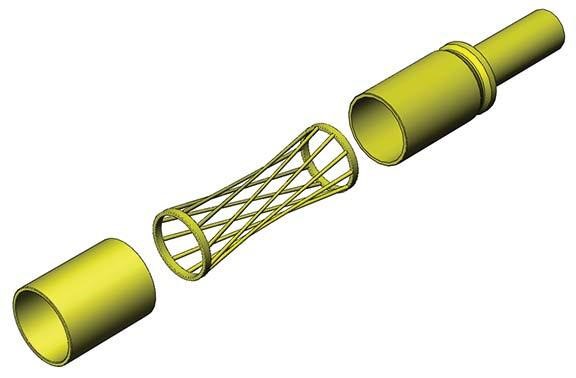
- VLIF (Very Low Insertion Force): Common sizes #22 and less average under one ounce per contact.
- Extraordinary Resistance to Shock & Vibration: Tests exceeding 300 g’s without discontinuity.
- Duty Cycle Exceeding 100,000 Mate/Demate: The burnishing action of the wires on the pin surface is non-destructive. Unlike the “plow” and scrape action of com-mon designs, HYPERBOLOID’s gentle mating action enhances life.
- Low, Low Contact Resistance: The multiplicity of line contact, as opposed to point contact in other designs, provides an excellent interface exhibiting low contact resistance (often less than 1/2 of MIL spec. allowanc-es). This characteristic also provides for a cooler run-ning contact under load.
- Improved Current Carrying Capacity: The low con-tact resistance gives a lower °C rise from ambient un-der load. This feature often allows the user to operate the same size contact under higher load.
- Highest Reliability: In use for over 40 years under the most demanding conditions HYPERBOLOID has proven itself to be the leading design for integrity and reliability. On space platforms, ships and boats at sea, land vehicles, fighter and transport aircraft, missiles, torpedoes, medical and transplant electronics, industrial and environmental controls, rail, construction, ATE and test equipment, PGA sockets, test interface stations, and other applications, HYPERBOLOID has lived up to its promise of the highest reliability connector available.
IEH CORPORATION HMM & HRM series use this technology
- HYPERBOLOID CONTACTS - August 5, 2019
0 comments on HYPERBOLOID CONTACTS