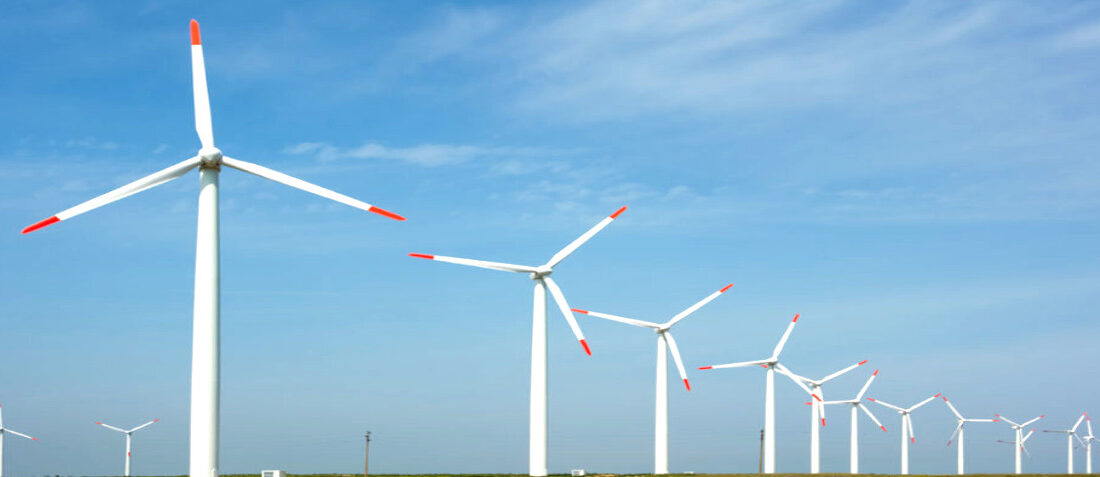
Reducing O&M costs with ultracapacitors
- Posted by doEEEt Media Group
- On November 27, 2020
- 0
Ultracapacitors are a reliable energy storage option that has resolved many of the typical pain points with battery-based systems.
While wind-farm operators work to optimize turbine performance and uptime, it’s inevitable that certain components will demand greater O&M attention. One aspect of turbine maintenance that typically causes multiple downtime hours per month is battery-based emergency pitch-control systems. Pitch control is an important turbine component used to operate and control the angle of blades to maximize wind generation. It also protects turbine blades from damage during excessive wind speeds or a grid power loss.
Replacing end-of-life or failed battery parts for emergency pitch-control backup systems in wind turbines is a time-consuming and costly process. It requires wind techs to climb up towers, and turbines to lose generating time. Ultracapacitor energy storage systems can eliminate scheduled pitch battery maintenance visits and significantly improve pitch system reliability.
This critical device is vital to successful turbine operation and fitted with energy storage backup power. However, site managers are too-often hit with unexpected maintenance costs relating to battery problems in pitch-control systems. These include degraded performance in cold and hot weather conditions, battery voltage faults, and up-tower climbs to replace failed battery systems.
How can site managers slash costly and time-consuming maintenance of the pitch system’s backup power? Ultracapacitors are a reliable energy storage option that has resolved many of the typical pain points with battery-based systems.
Chemistry uncovered
Ultracapacitors, also called supercapacitors, are high-powered energy storage devices that store charge electrostatically. In contrast, lead-acid batteries operate electrochemically, with inherent disadvantages due to the nature of their chemical process. As a result, ultracapacitors offer much greater efficiency and reliability in emergency pitch controls and require no scheduled maintenance for 10 years or longer. This contributes to greater turbine uptime.
For remote turbines in frigid, winter conditions or hot, summer temperatures, ultracapacitors’ electrostatic design makes for a wise choice. Here’s why: cold temperatures slow the rate of batteries’ chemical reactions, resulting in high internal resistance and inefficient charge acceptance. For example, a battery that provides 100% capacity at 80° F (27° C) will typically deliver only 50% capacity at 0° F (–18° C).
What’s more, each charge and discharge cycle requires electrochemical changes in the battery, causing the battery to lose capacity over time. Frigid conditions can render the battery ineffective. Extreme conditions may completely degrade battery performance, requiring operators to install multiple replacements.
Typically, pitch systems are fitted with environmental conditioning (heaters and fans) to keep batteries within their operating temperature range. However, wind farms still commonly experience premature battery failures from temperature extremes.
Battery-related pitch faults for turbine emergency pitch-control systems happen more than you might think. When consumer-owned electric cooperative, Iowa Lakes Electric Cooperative (ILEC), experienced problems with turbines at its wind farm, it switched to ultracapacitor-based energy storage.
The problem with pitch faults
Batteries are often the source of pitch faults as reported by SCADA systems, a turbine’s data-collection system. Battery voltage faults, one of several types of pitch faults, are specific to the turbine’s emergency pitch backup system. Voltage faults may occur during a battery load test, during battery charger failure, or when cold weather affects system performance and the battery fails to charge.
If the fault is unable to be repaired remotely, at least two wind technicians must climb up-tower to perform diagnostic inspections. Climbs are costly, complex, and offer an inherent safety risk. Repairs also result in turbine downtime and lost revenue.
Ultracapacitor retrofits
One way to overcome the limitations of lead-acid batteries in pitch-control systems is to replace the devices with ultracapacitor retrofit systems. Ultracapacitor storage modules provide a reliable and simplified emergency pitch-control backup system.
Ultracapacitor retrofits perform the same function as the battery system, with additional advantages.
- Ultracapacitors can withstand a pitch system’s load with minor voltage drop, compared to battery systems. After ultracapacitors are installed in a turbine’s pitch-control system and fully charged, subsequent recharges occur in a few minutes. This is unlike batteries, which may take about 20 to 30 minutes to recharge. In addition, ultracapacitors provide quick, high power even after long stretches of non-use. This is a performance advantage over batteries, which often fail after stretches of idle time.
- Ultracapacitors are available as “form-fit-functional” replacements for battery pitch systems, requiring zero modifications to the turbine hardware. Current ultracapacitor-based retrofit systems include an integrated charger and communication interface. This means the retrofit system can install in a timely manner. The ultracapacitor system check, voltage, and temperature are automatically reported to the turbine SCADA system in the same way the original battery system reports data, allowing for seamless plug-and-play functionality.
- The ultracapacitor-based system significantly reduces system failure rates, pitch system downtime, and unscheduled O&M costs. Ultracapacitor-based energy storage reduces the time spent maintaining and troubleshooting battery-based systems. Ultracapacitors require no scheduled maintenance over long periods of time and have much higher reliability, which means greater turbine uptime and project returns.
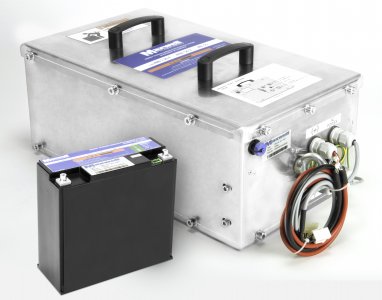
Maxwell Technologies’ ultracapacitor retrofit modules replace existing batteries for reliable and fail-safe pitch system performance; image credit: Maxwell Technologies
To remain competitive with other power generation sources, wind operators must ensure that turbines operate at maximum capacity. While batteries are optimal for long-term energy storage applications, the fast, high-power requirement of the pitch control function is best served with ultracapacitor energy storage.
Ultracapacitors improve chronic maintenance issues associated with battery-based systems and contribute to streamlined operations.
Source: Windpower Engineering & Development article
By Michelle Froese | August 27, 2018 , Joshua Hitt, Senior Product Line Manager Maxwell Technologies
- Managing EEE components for LEO and lower cost space missions - December 17, 2024
- Filtering Characteristics of Parallel-Connected Fixed Capacitors in LCC-HVDC - November 21, 2024
- ALTER SPACE TEST CENTER: testing approaches for New Space - September 30, 2024
0 comments on Reducing O&M costs with ultracapacitors