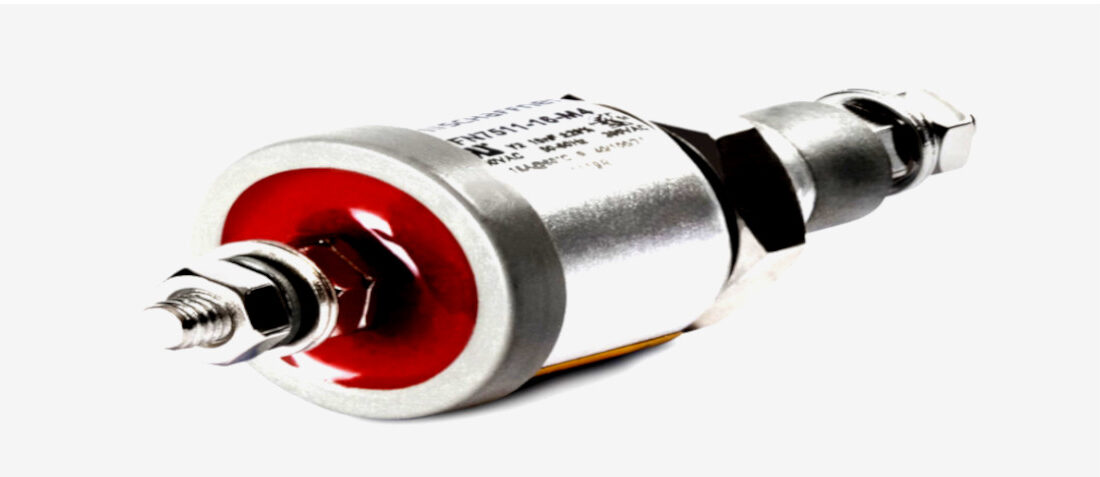
Feedthrough capacitors technology and applications
- Posted by doEEEt Media Group
- On October 3, 2020
- 0
Capacitor Geometry
One of the factors that greatly determine the performance characteristics of a capacitor is its geometry. The geometry of a typical feedthrough a capacitor differs from that of conventional capacitors. It is this structural difference that gives them their outstandingly good insertion loss characteristics. This low insertion loss is due to a design that ensures that the ground terminal side has zero residual inductance.
The current carrying conductor of a feedthrough capacitor is connected to an electrode that runs through the center of the component. The second electrode is contacted to its case. This concentric geometry is responsible for their outstanding performance characteristics. The special dimensioning of these components also help to ensure that their performance is excellent both at low and high frequencies.
In filtering applications, shunt inductance can significantly lower the filtering performance of a component. The series inductance in feedthrough capacitors ensures that these components have outstanding high-frequency performance. In addition, the geometry of feedthrough capacitors enhances their immunity to the undesirable effects of through current. Their high tolerance to these effects makes them one of the most reliable solutions for high frequency and high current filtering applications.
In filtering applications, shunt inductance can significantly lower the filtering performance of a component. The series inductance in feedthrough capacitors ensures that these components have outstanding high-frequency performance. In addition, the geometry of feedthrough capacitors enhances their immunity to the undesirable effects of through current. Their high tolerance to these effects makes them one of the most reliable solutions for high frequency and high current filtering applications.
The most common designs of feedthrough capacitors are discoidal and tubular feedthrough types. These two designs have slightly different performance characteristics, and it is important to consider these differences when selecting a component for your electronic circuit.
Soldering a capacitor to a printed circuit board can affect the performance characteristics of a component. Using alternative methods of attaching capacitors to circuit boards helps to eliminate the thermal stress associated with soldering. This results in better insertion loss and insulation resistance characteristics. Many manufacturers of feedthrough capacitors are increasingly adopting solder-free contacting technologies to improve the performance characteristics of their products. Solder-free feedthrough capacitors are usually compact and easy to install.
Tubular ceramic feedthrough capacitors
Tubular feedthrough capacitors are widely used in high-frequency filtering applications. For these capacitors, the inductance is in the series arm of the filter. Due to their cylindrical design, the insertion loss of these capacitors is uniform over a wide range of temperatures. Compared to other wound capacitors, the unique structure of these components yields an impressively low inductance.
The internal structure of ceramic tubular feedthrough capacitors varies depending on the desired performance characteristics and the applications they are intended for. Solid feedthrough capacitors are commonly used for low-cost applications. These components do not have internal electrodes.
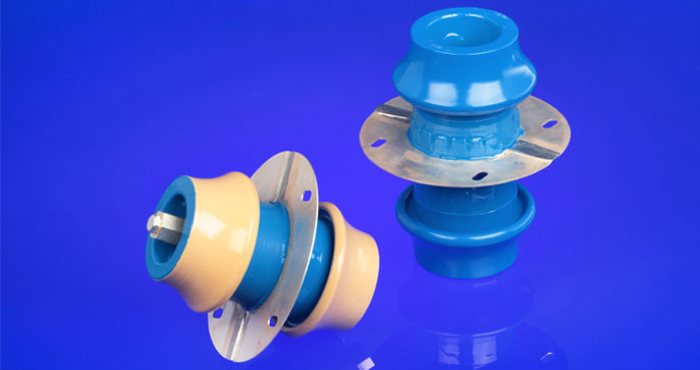
Fig.1.RF Feedthrough Capacitor example; image credit. CeramTec
Some filtering applications demand capacitors with high capacitance to volume ratio. Multilayer tubular feedthrough capacitors offer high capacitance to volume ratio, and this makes them a suitable choice for low-frequency filtering applications. These components are also widely used in circuits with high source impedances. In addition to conventional designs, many capacitor manufacturers produce specialty tubular components on demand.
Discoidal feedthrough capacitors
Discoidal feedthrough capacitors are widely used in the EMI filter industry. These components come in different designs and in a wide range of capacitance ratings to meet the diverse requirements of today’s applications. In addition, most of these components are compact in size and have impressive dielectric strength.
Compared to conventional capacitors, the special construction of ceramic discoidal feedthrough capacitors yields low inductance. Their circular geometry ensures low impedance since there are multiple paths to ground. The impressive performance characteristics of these components make them a suitable choice for high-frequency applications. These feedthrough capacitors are mostly used for filtering and bypass applications.
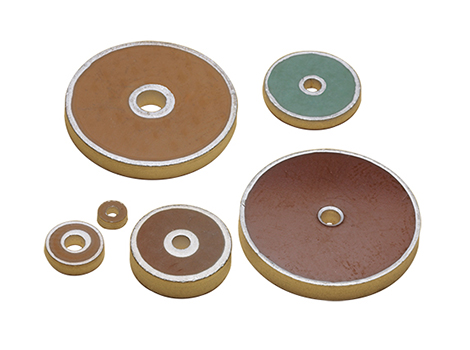
Fig.2. Discoidal feedthrough capacitors example; image credit: API technologies corp
Plastic film feedthrough capacitors
Metalized film feedthrough capacitors are commonly used in applications that demand components with high reliability. These capacitors utilize metalized plastic film construction technology to deliver the required high reliability. Just like ordinary metalized film capacitors, these feedthrough capacitors have self-healing properties. In addition to high reliability, these components also offer impressive high-frequency performance.
Just like ceramic feedthrough capacitors, these components do not have lead inductance. This means that, unlike ordinary capacitors, they don’t have major resonance. Moreover, the capacitance per unit volume of these components is impressively high.
The cost of a component is one of the main factors that electronic designers consider when selecting a capacitor for a particular application. Film feedthrough capacitors are cost-effective solutions, and this makes them a popular choice for many applications. Plastic film feedthrough capacitors are available in a broad array of ratings and capacitance-voltage combinations.
Heat can significantly reduce the life and reliability of plastic film capacitors. Most manufacturers of film feedthrough capacitors are producing solderless components to eliminate the negative effects of soldering. Plastic film feedthrough capacitors are suitable for a wide range of filtering applications, and they are common elements in electronic circuits for base stations, servers, and switches.
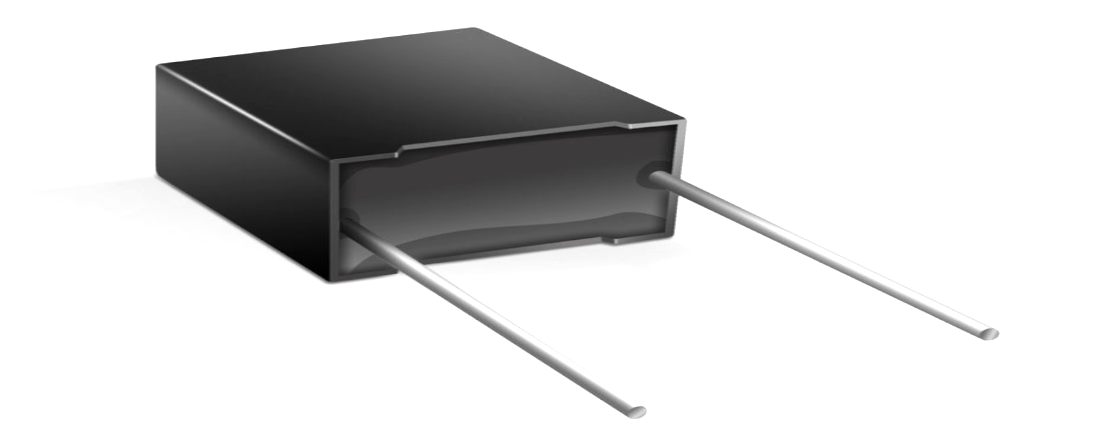
Fig.3. Plastic film EMI/EMC feedthrough capacitors
Surface Mount Feedthrough Filters
SMD feedthrough filters are an easy way to achieve broadband EMI reduction in a small SMD package. SMD feedthru filters can help reduce cost designs by eliminating some types of L/C filters, increasing system reliability and saving valuable PCB area. SMD feedthru filters are offered in both 0805, 1206 single element packages or in 1206 four element packages. The unique construction of a feedthru capacitor provides low parallel inductance and offers excellent decoupling capability for all high di/dt environments and provides significant noise reduction in digital circuits
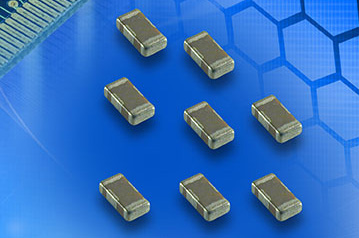
Fig.4. SMD feedthrough filters example; image credit: AVX
There are various types available, optimized per application specifics such as High current feedthrough capacitors designed to have high current handling capability within a capacitance range up to 100,000pF and a current rating up to 5A. The W2H feedthrough filters can replace some discrete L/C filter networks in miniature SMD design.
Applications of feedthrough capacitors
Standard capacitors are not suitable for filtering applications because they tend to introduce high impedance. This impedance, usually in the form of shunt inductance, is undesirable and can significantly affect the performance of a filtering circuit. In comparison, feedthrough capacitors do not have this undesirable inductance in the shunt branch of a filter. The inductance of these components is in the series branch.
Feedthrough capacitors are commonly used in today’s AC/DC supply lines to suppress harmful interference. They are also widely used in electronic circuits for base stations, telephone exchanges, shielded rooms, power supplies, and so on.
RF feedthrough capacitors are mostly used for high power applications such as dielectric and induction heating equipment, plasma generators, and radio broadcast transmitters. They are also widely used for matching high power tuned circuits, bypassing and coupling RF circuits, and coupling antenna circuits.
SMT feedthrough capacitors are suitable for a wide range of applications including the following: power decoupling in amplifier circuits, high frequency decoupling in power lines, filtering in digital to RF interfacing circuits, voltage conditioning in RF amplification circuits, and high frequency decoupling in data, clock, and control lines.
Source: Capacitor Faks blog
This post was prepared using a blog by Anthony Kenny from Capacitor Faks with introduction an overview of feedthrough capacitors technologies, types and some typical applications.
- Managing EEE components for LEO and lower cost space missions - December 17, 2024
- Filtering Characteristics of Parallel-Connected Fixed Capacitors in LCC-HVDC - November 21, 2024
- ALTER SPACE TEST CENTER: testing approaches for New Space - September 30, 2024
0 comments on Feedthrough capacitors technology and applications